Preparation method of 3,5-di (trifluoromethyl) benzoyl chloride and new 3,5-di trihalomethyl benzoylate A and 3,5-dimethyl benzoylate A
A technology of benzoyl chloride and trifluoromethyl, used in the preparation of 3,5-bis(trifluoromethyl)benzoyl chloride and new 3,5-bis(trihalomethyl)- and 3, In the field of 5-dimethylbenzoyl halide, it can solve problems such as huge expenses
- Summary
- Abstract
- Description
- Claims
- Application Information
AI Technical Summary
Problems solved by technology
Method used
Image
Examples
Embodiment 1
[0070] 3,5-Dimethylbenzoyl chloride
[0071] First, 1000 g of 3,5-dimethylbenzoic acid in 450 ml of toluene was placed in a 4-liter flat-bottomed reaction vessel, and 80 ml of thionyl chloride was added dropwise at 60° C. for 2 hours under stirring to generate gas. The mixture was then heated to boiling (internal temperature 102°C) and refluxed for 2 hours. Excess thionyl chloride and some toluene were then distilled off at atmospheric pressure at a top temperature of up to 102° C. during 1.5 hours. The mixture was allowed to cool to 80°C and the toluene was distilled off, this time at 20 mbar. The residue was distilled off at 20 mbar up to a boiling point of 110° C. (in the still) column. The residue obtained was 1092 g (96.7% of theory) of 3,5-dimethylbenzoyl chloride.
Embodiment 2
[0073] 3,5-Bis(trichloromethyl)benzoyl chloride
[0074] At 120°C, 1092g of 3,5-dimethylbenzoyl chloride was first added to a reaction vessel equipped with an air-cooled UV immersion lamp. Under UV radiation, a total amount of 4340g of chlorine was introduced during 61 hours, and the temperature rose steadily. up to 180°C. At this point 100% of the starting material had reacted according to GC analysis. After blowing off the excess chlorine with nitrogen, 2390 g (98.1% of theory) of 3,5-bis(trichloromethyl)benzoyl chloride remained.
Embodiment 3
[0076] 3,5-bis(trifluoromethyl)benzoyl fluoride
[0077] First, 990 ml of anhydrous hydrofluoric acid were added to a 5 liter stainless steel stirred autoclave equipped with a sloped condenser (operated at -10°C with coolant) and a pressure regulator. Then, 1126 g of 3,5-bis(trichloromethyl)benzoyl chloride were added dropwise during 30 minutes at -5 to 0°C, with only slight generation of hydrogen chloride gas. Allow the temperature to rise to +20°C. When the slight gas evolution had ended (after 1.5 hours), 68 g of titanium tetrachloride were added during 40 minutes. When the new gas evolution subsides (after 2 hours), seal the equipment, inject nitrogen to 10 bar, gradually heat the equipment to 140° C., and continuously depressurize the generated hydrogen chloride at 25 bar. After 11 hours at 140°C, the reaction was complete. The autoclave was cooled and decompressed, excess hydrogen fluoride (248 g) was distilled off at atmospheric pressure, and the residue was distille...
PUM
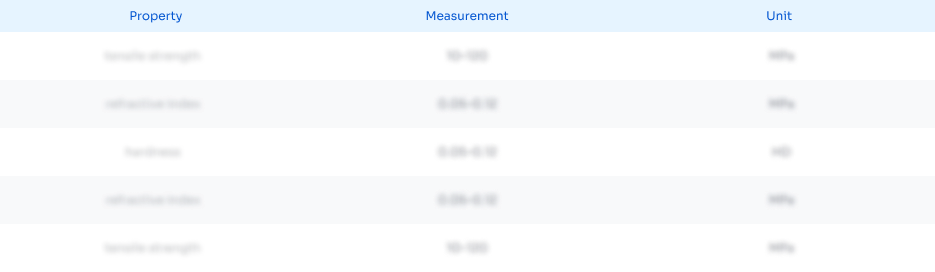
Abstract
Description
Claims
Application Information

- R&D Engineer
- R&D Manager
- IP Professional
- Industry Leading Data Capabilities
- Powerful AI technology
- Patent DNA Extraction
Browse by: Latest US Patents, China's latest patents, Technical Efficacy Thesaurus, Application Domain, Technology Topic, Popular Technical Reports.
© 2024 PatSnap. All rights reserved.Legal|Privacy policy|Modern Slavery Act Transparency Statement|Sitemap|About US| Contact US: help@patsnap.com