Steady-pressure energy-saving backwashing method for heating surface of three-waste furnace
A three-waste furnace and backwashing technology, applied in washing, separation methods, chemical instruments and methods, etc., can solve problems such as poor water circulation, large pressure fluctuations, and large water consumption, achieve recycling and reuse, reduce pump start-up, etc. The number of stops and the effect of improving flushing efficiency
- Summary
- Abstract
- Description
- Claims
- Application Information
AI Technical Summary
Problems solved by technology
Method used
Image
Examples
Embodiment Construction
[0014] See figure 1 , A method for backwashing the heating surface of a three-waste furnace with constant pressure and energy saving, characterized in that it comprises the following steps:
[0015] a. Use a pressurized pump to bring the flushing water to the water tank of the deaerator to a high water level for heating and deoxygenation, and the water temperature is controlled at 90 to 100 ° C, and the flushing water is PH8.8-9.3 with ammonia added and desalinated water;
[0016] b. Feed the above-mentioned heating and deoxidized water into the three-waste boiler from the backwash valve of the superheater, and control the flow rate to 20~45t / h. When the steam drum of the three-waste boiler is full of water, turn off the water supply pump and let it soak for 1.5 hours;
[0017] c. After the static bubble is over, open the fixed discharge valve, start the water supply pump to flush with water, and the rinsed water is discharged to the circulating water pool through the fixed di...
PUM
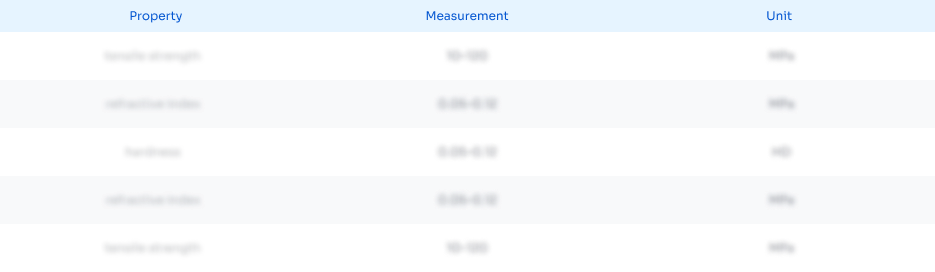
Abstract
Description
Claims
Application Information

- R&D
- Intellectual Property
- Life Sciences
- Materials
- Tech Scout
- Unparalleled Data Quality
- Higher Quality Content
- 60% Fewer Hallucinations
Browse by: Latest US Patents, China's latest patents, Technical Efficacy Thesaurus, Application Domain, Technology Topic, Popular Technical Reports.
© 2025 PatSnap. All rights reserved.Legal|Privacy policy|Modern Slavery Act Transparency Statement|Sitemap|About US| Contact US: help@patsnap.com