Method for recovering ethylene glycol in waste liquid
A recovery method, ethylene glycol technology, applied in chemical instruments and methods, preparation of organic compounds, organic chemistry, etc., can solve problems such as poor applicability, high processing costs, and large property gaps, and reduce heating time and heating area Large, meet the effect of rapid heating
- Summary
- Abstract
- Description
- Claims
- Application Information
AI Technical Summary
Problems solved by technology
Method used
Image
Examples
Embodiment 1
[0048] (1) open the peristaltic pump-4 and pump the stock solution into the stock solution preheating device 5 at a rate of 500mL / min, and the temperature of the circulating heating device-3 is set to 195 ° C; flow into the stock solution evaporation tank 9, then close the valve two 10, open Stirrer 8, vacuum pump 2 27, refrigeration pump 2 28 and circulating heating device 2 12; the vacuum degree is set to 30000Pa, and the temperature of the refrigeration pump is 10°C; The holding temperature was set to 90°C.
[0049] (2) When the temperature of the waste liquid is raised to 90°C, open valve-7, at this time, substances with boiling points lower than ethylene glycol, such as water, glycolaldehyde, glyoxal, and glycolic acid, begin to evaporate in large quantities and are condensed by condensing device-2 Collected into the recycling material storage tank 1; when the solution conductivity detector 6 monitors that the solution conductivity does not change for more than 10 minutes...
Embodiment 2
[0052] (1) open the peristaltic pump-4 and pump the stock solution into the stock solution preheating device 5 at a rate of 500mL / min, and the temperature of the circulating heating device-3 is set to 195 ° C; flow into the stock solution evaporation tank 9 subsequently, close the valve two 10, open stirring 8. The second vacuum pump 27, the second refrigeration pump 28 and the second circulation heating device 12; the vacuum degree is set to 30000Pa, and the temperature of the refrigeration pump is 10 °C; Set to 90°C.
[0053] (2) When the temperature of the stock solution is raised to 90°C, open valve-7, at this time, substances with boiling points lower than ethylene glycol, such as water, glycolaldehyde, glyoxal, and glycolic acid, begin to evaporate in large quantities and are condensed and collected by condenser-2 To the reclaimed material storage tank 1; when the solution conductivity detector 6 monitors that the solution conductivity does not change for more than 10 mi...
Embodiment 3
[0055] (1) open the peristaltic pump-4 and pump the stock solution into the stock solution preheating device 5 at a rate of 500mL / min, and the temperature of the circulating heating device-3 is set to 195 ° C; flow into the stock solution evaporation tank 9 subsequently, close the valve two 10, open stirring 8. The second vacuum pump 27, the second refrigeration pump 28 and the second circulating heating device 12; set the vacuum degree to normal pressure, and the temperature of the refrigeration pump to be 10 °C; The temperature was set at 195°C.
[0056] (2) When the temperature of the waste liquid is raised to 195°C, open valve-7. At this time, substances with boiling points lower than ethylene glycol, such as water, glycolaldehyde, glyoxal, and glycolic acid, begin to evaporate in large quantities and condense through condenser-2. Collect to the reclaimed material storage tank 1; when the solution conductivity detector 6 monitors that the solution conductivity does not cha...
PUM
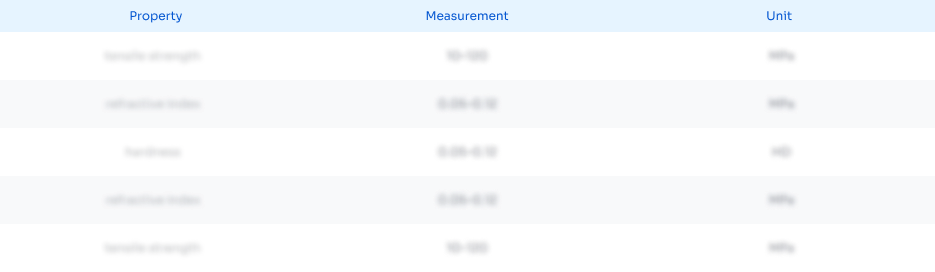
Abstract
Description
Claims
Application Information

- R&D
- Intellectual Property
- Life Sciences
- Materials
- Tech Scout
- Unparalleled Data Quality
- Higher Quality Content
- 60% Fewer Hallucinations
Browse by: Latest US Patents, China's latest patents, Technical Efficacy Thesaurus, Application Domain, Technology Topic, Popular Technical Reports.
© 2025 PatSnap. All rights reserved.Legal|Privacy policy|Modern Slavery Act Transparency Statement|Sitemap|About US| Contact US: help@patsnap.com