Lightweight ceramsite fired from solid waste and method thereof
A solid waste and lightweight ceramsite technology, which is applied in the field of solid waste resource utilization, can solve the problems of low content and low content, limit the production scale of light ceramsite, and difficulty in obtaining it, so as to achieve low cost, Good roasting process performance and high production efficiency
- Summary
- Abstract
- Description
- Claims
- Application Information
AI Technical Summary
Problems solved by technology
Method used
Image
Examples
Embodiment 1
[0067] S1. Material preparation: Select the original raw materials of gold tailings, the original raw materials of waste incineration fly ash and the polluted soil that has been dried and ground for use.
[0068] S2, prepared into a nucleus:
[0069] S21. According to the parts by mass, transfer 74 parts of original raw materials of gold tailings, 9 parts of original raw materials of waste incineration fly ash and 17 parts of polluted soil into a pre-wet mixer for mixing;
[0070] S22. During the stirring process, add an appropriate amount of tap water into the pre-wet mixer to obtain a wet material with a water content of 10% (that is, the water content of the wet material is 1 / 2 of the water content of the wet raw pellets).
[0071] S23. Continue stirring the wet material to obtain a mixture containing spherical cores.
[0072] S3, ball screening: transfer the mixture in step S2 into a disc balling machine, and adjust and prepare the same amount of tap water as in step S2 d...
Embodiment 2
[0079] S1. Material preparation: Select the original raw materials of gold tailings, the original raw materials of waste incineration fly ash and the polluted soil that has been dried and ground for use.
[0080] S2, prepared into a nucleus:
[0081] S21. Transfer 70 parts of raw gold tailings raw materials, 13 parts of waste incineration fly ash raw materials, and 17 parts of polluted soil to a pre-wet mixer for stirring according to parts by mass.
[0082] S22. During the stirring process, add an appropriate amount of tap water to the pre-wet mixer to obtain a wet material with a water content of 11% (that is, the water content of the wet material is 1 / 2 of the water content of the wet raw pellets).
[0083] S23. Continue stirring the wet material to obtain a mixture containing spherical cores.
[0084] S3, ball screening: transfer the mixture in step S2 into a disc balling machine, and adjust and prepare the same amount of tap water as in step S2 during the rolling process...
Embodiment 3
[0091] S1. Material preparation: Select the original raw materials of gold tailings, the original raw materials of waste incineration fly ash and the polluted soil that has been dried and ground for use.
[0092] S2, prepared into a nucleus:
[0093] S21. According to the parts by mass, transfer 66 parts of raw gold tailings raw materials, 17 parts of raw materials of waste incineration fly ash and 17 parts of polluted soil into a pre-wet mixer for stirring.
[0094] S22. During the stirring process, add an appropriate amount of tap water into the pre-wet mixer to obtain a wet material with a water content of 12% (that is, the water content of the wet material is 1 / 2 of the water content of the wet raw pellet).
[0095] S23. Continue stirring the wet material to obtain a mixture containing spherical cores.
[0096] S3, ball screening: transfer the mixture in step S2 into a disc balling machine, and adjust and prepare the same amount of tap water as in step S2 during the rolli...
PUM
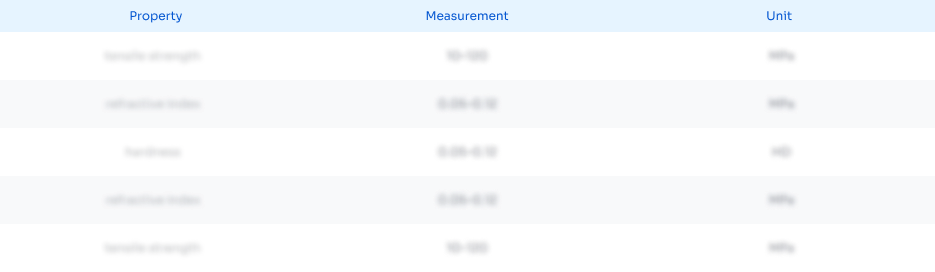
Abstract
Description
Claims
Application Information

- R&D Engineer
- R&D Manager
- IP Professional
- Industry Leading Data Capabilities
- Powerful AI technology
- Patent DNA Extraction
Browse by: Latest US Patents, China's latest patents, Technical Efficacy Thesaurus, Application Domain, Technology Topic, Popular Technical Reports.
© 2024 PatSnap. All rights reserved.Legal|Privacy policy|Modern Slavery Act Transparency Statement|Sitemap|About US| Contact US: help@patsnap.com