Method for extracting lithium from lithium ore leaching residues
A technology for leaching slag and lithium ore, which is applied in the direction of improving process efficiency, etc., to achieve the effects of saving resources, effectively recycling, and ensuring high-efficiency utilization
- Summary
- Abstract
- Description
- Claims
- Application Information
AI Technical Summary
Problems solved by technology
Method used
Image
Examples
Embodiment 1
[0047] A spodumene leaching slag contains 0.55% lithium oxide, using figure 2 The process flow shown, the specific parameters are shown in Table 1 below:
[0048]
[0049]
[0050] Table 1
[0051] In the present embodiment, the method for extracting lithium from the above-mentioned lithium ore leaching slag provided by the present invention is used to process the spodumene leaching slag, and the test results are shown in Table 2 below:
[0052]
[0053] Table 2
Embodiment 2
[0055]The leaching slag of a certain lithoferrite contains 0.7% lithium oxide, using figure 2 The technical process shown, the specific parameters are shown in Table 3 below:
[0056]
[0057]
[0058] table 3
[0059] In the present embodiment, the method for extracting lithium from the above-mentioned lithium ore leaching slag provided by the present invention is used to process the lithoferite leaching slag, and the test results are shown in Table 4 below:
[0060]
[0061] Table 4
Embodiment 3
[0063] A lepidolite leaching slag contains 0.45% lithium oxide, using figure 2 The process flow shown, the specific parameters are shown in Table 5 below:
[0064]
[0065] table 5
[0066] In the present embodiment, the method for extracting lithium from the above-mentioned lithium ore leaching slag provided by the present invention is used to process the lepidolite leaching slag, and the test results are shown in Table 6 below:
[0067]
[0068] Table 6
PUM
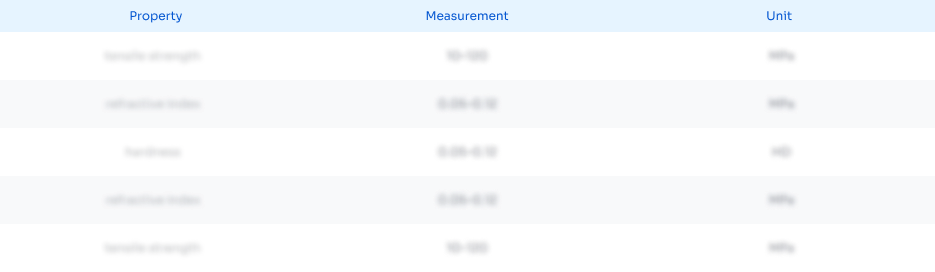
Abstract
Description
Claims
Application Information

- Generate Ideas
- Intellectual Property
- Life Sciences
- Materials
- Tech Scout
- Unparalleled Data Quality
- Higher Quality Content
- 60% Fewer Hallucinations
Browse by: Latest US Patents, China's latest patents, Technical Efficacy Thesaurus, Application Domain, Technology Topic, Popular Technical Reports.
© 2025 PatSnap. All rights reserved.Legal|Privacy policy|Modern Slavery Act Transparency Statement|Sitemap|About US| Contact US: help@patsnap.com