Short glass fiber reinforced epoxy foam and preparation method thereof
A technology of short glass fiber and chopped glass fiber, which is applied in the field of short glass fiber reinforced epoxy foam and its preparation, which can solve the problems of insufficient temperature resistance, inability to directly foam molding, high cost of PMI foam, etc., and reach the production cycle Short, suitable for large-scale production, low price effect
- Summary
- Abstract
- Description
- Claims
- Application Information
AI Technical Summary
Problems solved by technology
Method used
Image
Examples
Embodiment 1
[0028] 70kg / m3 foam formula:
[0029] Epoxy resin E-51 100 parts by weight
[0030] Triethylenetetramine curing agent 3 parts by weight
[0031] Isocyanate PAPI 280 parts by weight
[0032] 0.3% of the amount of dibutyltin dilaurate PAPI used
[0033] 3 parts water
[0034] Fumed silica 3% of epoxy resin
[0035] 5% of 3mm chopped glass fiber PAPI
[0036] Preparation Process:
[0037] Step 1: Weigh epoxy resin, add organotin compound, water and curing agent in proportion, stir evenly with a mixer, grind twice with three rollers, and then vacuum degas to obtain mixture A;
[0038] Step 2: Add fumed silica to mixture A, stir it with a mixer until there is no dry powder, and then grind it three times with a three-roller mill. During the grinding process, the distance between the grinding rollers should be controlled to 0.5-1mm to avoid damage to the fumed silica. Vacuum The defoaming port obtains mixture B;
[0039] The third step: weigh the isocyanate, add chopped glass...
Embodiment 2
[0045] 110kg / m3 foam formula:
[0046] Epoxy resin E-51 100 parts by weight
[0047] Triethylenetetramine curing agent 3 parts by weight
[0048] Isocyanate PAPI 280 parts by weight
[0049] 0.3% of the amount of dibutyltin dilaurate PAPI used
[0050] Water 1.5 parts by weight
[0051] Fumed silica 3% of epoxy resin
[0052] 5% of 3mm chopped glass fiber PAPI
[0053] The preparation process and epoxy foam curing system are the same as those in Example 1, and the density, glass transition temperature and mechanical properties of the epoxy foam are shown in Table 2.
Embodiment 3
[0055] 200kg / m3 foam formula:
[0056] Epoxy resin E-51 100 parts by weight
[0057] Triethylenetetramine curing agent 3 parts by weight
[0058] Isocyanate PAPI 300 parts by weight
[0059] 0.3% of the amount of dibutyltin dilaurate PAPI used
[0060] Water 1.5 parts by weight
[0061] Fumed silica 3% of epoxy resin
[0062] 5% of 3mm chopped glass fiber PAPI
[0063] The preparation process and epoxy foam curing system are the same as those in Example 1, and the density, glass transition temperature and mechanical properties of the epoxy foam are shown in Table 2.
PUM
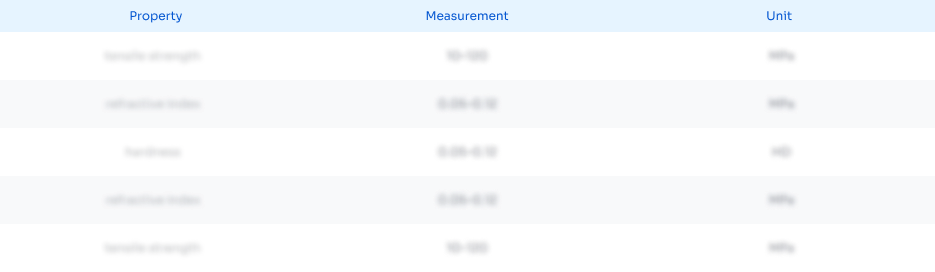
Abstract
Description
Claims
Application Information

- R&D Engineer
- R&D Manager
- IP Professional
- Industry Leading Data Capabilities
- Powerful AI technology
- Patent DNA Extraction
Browse by: Latest US Patents, China's latest patents, Technical Efficacy Thesaurus, Application Domain, Technology Topic, Popular Technical Reports.
© 2024 PatSnap. All rights reserved.Legal|Privacy policy|Modern Slavery Act Transparency Statement|Sitemap|About US| Contact US: help@patsnap.com