Precious metal catalyst for catalytic oxidation of CO and preparation method thereof
A precious metal catalyst, catalytic oxidation technology, applied in the field of environmental engineering, can solve the problems of low activation temperature, sulfur resistance and water resistance, low activation temperature, etc., to improve the service life, facilitate large-scale production and market promotion Applied, easily reproducible effects
- Summary
- Abstract
- Description
- Claims
- Application Information
AI Technical Summary
Problems solved by technology
Method used
Image
Examples
Embodiment 1
[0024] Weigh 27g of titanium dioxide, add 0.5g of chloroplatinic acid, pre-mix evenly, add the material into the ball mill jar, weigh 0.4g of tin protochloride, quickly add it into the ball mill jar, use a planetary ball mill, at 300r / Under the condition of rotating speed of min, ball mill clockwise for 20 minutes, then increase the rotating speed to 480r / min, and ball mill counterclockwise for 50 minutes. After the ball milling, take out the catalyst powder and roast it in a muffle furnace at 400°C for 2.5 hours. After the catalyst was cooled to room temperature, it was stored dry and sealed for use, and recorded as 1#.
Embodiment 2
[0026] Weigh 23.5g of titanium dioxide, add 0.5g of chloroplatinic acid, pre-mix evenly, add the materials into the ball mill jar, weigh 0.73g of stannous chloride and 0.025g of iron oxide, quickly add them into the ball mill jar, and use planetary Type ball mill, at the speed of 250r / min, mill clockwise for 35 minutes, then increase the speed to 520r / min, and mill counterclockwise for 35 minutes. Under roasting 2h. After the catalyst was cooled to room temperature, it was stored dry and sealed for use, and recorded as 2#.
PUM
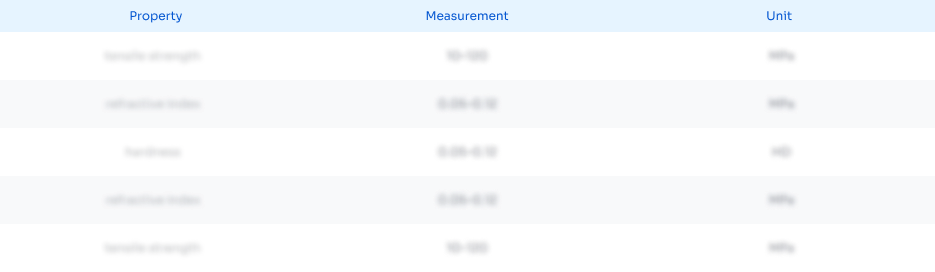
Abstract
Description
Claims
Application Information

- R&D Engineer
- R&D Manager
- IP Professional
- Industry Leading Data Capabilities
- Powerful AI technology
- Patent DNA Extraction
Browse by: Latest US Patents, China's latest patents, Technical Efficacy Thesaurus, Application Domain, Technology Topic, Popular Technical Reports.
© 2024 PatSnap. All rights reserved.Legal|Privacy policy|Modern Slavery Act Transparency Statement|Sitemap|About US| Contact US: help@patsnap.com