Delustering master batch for plastic and preparation method thereof
A technology for matting masterbatch and plastics, which is applied in the field of plastic processing and can solve the problems of affecting mechanical properties, reducing the mechanical properties of matting masterbatches, and difficult to disperse inorganic matting agents evenly.
- Summary
- Abstract
- Description
- Claims
- Application Information
AI Technical Summary
Problems solved by technology
Method used
Image
Examples
Embodiment 1
[0032] Extinct hyperbranched polymers are made by the following steps:
[0033]i. 0.1mol 4-hydroxybenzaldehyde, 0.2mol 4-hydroxyacetophenone, 0.21mol ammonium acetate and 300mL glacial acetic acid were stirred and heated to reflux, reacted for 3h, cooled to room temperature and poured into aqueous acetic acid (volume of acetic acid) The fraction is 50%) and precipitated, stirred for 10 min, filtered with suction, the crude product was recrystallized twice with absolute ethanol, and dried in vacuo to obtain 2,4,6-tris(4-hydroxyphenyl)pyridine;
[0034] ii. After mixing 0.1mol 2-(2'-hydroxy-5-methylphenyl)benzotriazole, 0.99g p-toluenesulfonic acid and 80mL tetrahydrofuran, then add 0.1mol 3-hydroxy-2-(hydroxyl Methyl)propionic acid, heated under reflux for 6 h, stopped the reaction, spin-dried, then dissolved in 80 mL of dichloromethane, washed with water several times, combined the organic phases, spin-evaporated, and dried to obtain a light-absorbing diol;
[0035] iii. Add ...
Embodiment 2
[0038] Extinct hyperbranched polymers are made by the following steps:
[0039] i. 0.1mol 4-hydroxybenzaldehyde, 0.2mol 4-hydroxyacetophenone, 0.23mol ammonium acetate and 300mL glacial acetic acid were stirred and heated to reflux, reacted for 3h, cooled to room temperature and poured into aqueous acetic acid (volume of acetic acid) The fraction is 50%) and precipitated, stirred for 10 min, filtered with suction, the crude product was recrystallized twice with absolute ethanol, and dried in vacuo to obtain 2,4,6-tris(4-hydroxyphenyl)pyridine;
[0040] ii. After mixing 0.1mol 2-(2'-hydroxy-5-methylphenyl)benzotriazole, 1.45g p-toluenesulfonic acid and 80mL tetrahydrofuran, then add 0.1mol 3-hydroxy-2-(hydroxyl Methyl)propionic acid, heated under reflux for 6 h, stopped the reaction, spin-dried, then dissolved in 80 mL of dichloromethane, washed with water several times, combined the organic phases, spin-evaporated, and dried to obtain a light-absorbing diol;
[0041] iii. Add...
Embodiment 3
[0044] Preparation of composite matting agent (inorganic matting agent with matting hyperbranched polymer grafted on the surface):
[0045] (1) At room temperature, ultrasonically disperse 3g KH560 in 80mL aqueous ethanol solution, then add 15g titanium dioxide powder, ultrasonically disperse for 15min, suction filter, wash with absolute ethanol, and dry to obtain epoxidized titanium dioxide, and the ethanol solution is composed of ethanol and water according to volume The ratio of 5:3 mixed composition;
[0046] (2) 10g of epoxidized titanium dioxide and 1.5g of the extinction hyperbranched polymer prepared in Example 1 were added to 80mL of ethanol, stirred for 3h, then heated to reflux, stopped stirring, and reacted under reflux for 1h, then cooled down and rotated and evaporated with ethanol Washed twice and dried in vacuum to obtain a composite matting agent.
PUM
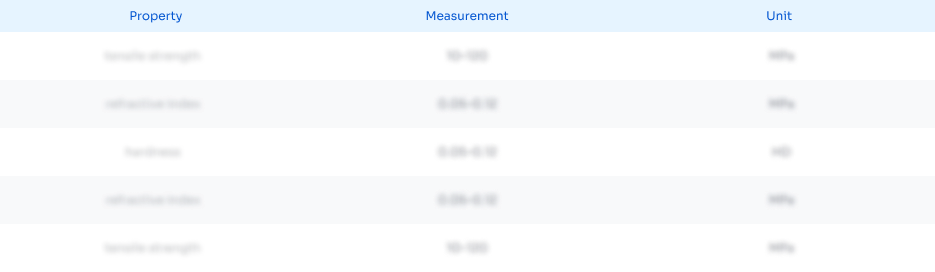
Abstract
Description
Claims
Application Information

- R&D
- Intellectual Property
- Life Sciences
- Materials
- Tech Scout
- Unparalleled Data Quality
- Higher Quality Content
- 60% Fewer Hallucinations
Browse by: Latest US Patents, China's latest patents, Technical Efficacy Thesaurus, Application Domain, Technology Topic, Popular Technical Reports.
© 2025 PatSnap. All rights reserved.Legal|Privacy policy|Modern Slavery Act Transparency Statement|Sitemap|About US| Contact US: help@patsnap.com