Device and method for improving workpiece edge collapse problem through closed-loop control of laser power
A technology of laser power and closed-loop control, which is applied to the improvement of process efficiency, additive manufacturing, and additive processing. It can solve the problems of workpiece sagging, affecting the surface quality and mechanical properties of the workpiece, so as to prolong the service life and improve the collapse of the workpiece. Side issues, inhibiting cumulative effects
- Summary
- Abstract
- Description
- Claims
- Application Information
AI Technical Summary
Problems solved by technology
Method used
Image
Examples
Embodiment 1
[0050] On the software control integrated platform on the PC side, set the laser control mode to manual, click the record button, and the directional energy deposition equipment starts to work. Monitor and measure real-time melt width curve and power during deposition and manufacturing, and draw curves such as figure 2 shown.
Embodiment 2
[0052] On the software control integrated platform on the PC side, set the laser control mode to automatic, the reference track parameter to 3, the initial power setting to 2000W, the process power limit to the maximum value of 5000W, the minimum value of 500W, the pixel ratio to 0.333, the threshold value to 1025, and the PID parameter setting. for K P : 200,K I : 500,K D : 100, camera status: connected, laser status: on, the number of single-layer deposition tracks is 12, and the automatic learning number n of the control algorithm is set to 3.
[0053] When depositing the 1st to 3rd tracks, set the first melt pool width detected in the traditional mode as the reference melt width, and use the detected real-time melt width W r (k) and the reference value melting width W i The difference e(k) of (k) is used as the input variable of the PID controller:
[0054] e(k)=W i (k)-W r (k);
[0055] Among them, W i (k) is the reference melting width, W r (k) is the real-time ...
PUM
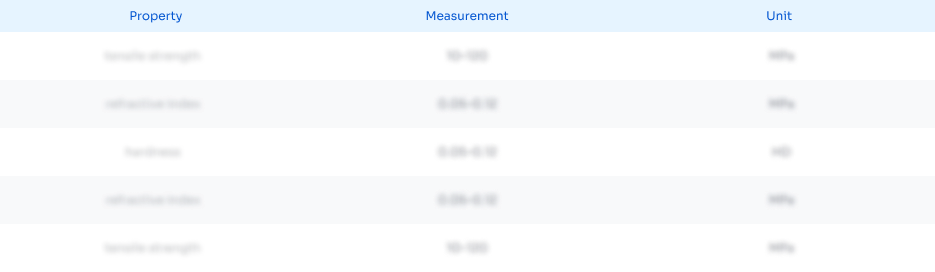
Abstract
Description
Claims
Application Information

- Generate Ideas
- Intellectual Property
- Life Sciences
- Materials
- Tech Scout
- Unparalleled Data Quality
- Higher Quality Content
- 60% Fewer Hallucinations
Browse by: Latest US Patents, China's latest patents, Technical Efficacy Thesaurus, Application Domain, Technology Topic, Popular Technical Reports.
© 2025 PatSnap. All rights reserved.Legal|Privacy policy|Modern Slavery Act Transparency Statement|Sitemap|About US| Contact US: help@patsnap.com