Numerical control machine tool cutting stability prediction and optimization method considering parameter uncertainty
A technology of stability prediction and CNC machine tools, which is applied in the field of CNC machine tools, can solve the problems of conservatism and low reliability of stable domain boundaries, and achieve the effect of improving accuracy and improving the economic benefits of manufacturers
- Summary
- Abstract
- Description
- Claims
- Application Information
AI Technical Summary
Problems solved by technology
Method used
Image
Examples
Embodiment
[0050] Such as figure 1 As shown, one aspect of the present invention provides a method for predicting the cutting stability of a numerically controlled machine tool considering parameter uncertainties, comprising the following steps: defining the machine tool as a chain structure product structure model formed by connecting the key components with a joint, and Construct the functional structure model of the chain structure product through a software simulation platform; add constraints including machine tool pose and spindle speed to the software simulation platform to complete the construction of a generalized dynamic machining space machine tool finite element model, expressing The relationship between the machining state of the CNC machine tool and the structural dynamics characteristics; relying on the finite element model of the machine tool in the generalized dynamic machining space, the influencing factors including the frequency response function of the machining point...
example 1
[0086] A method for predicting cutting stability of CNC machine tools considering uncertain parameters includes steps (1) and (2).
[0087] (1) Comprehensively adopt finite element technology, numerical simulation technology and other means to construct a generalized dynamic machining space CNC machine tool finite element model suitable for cutting stability prediction: ① During the cutting process of the machine tool, the tool processing position (that is, the machine position A kind of attitude) and the change of the spindle speed change the dynamic characteristics of the machine tool structure, resulting in uncertainty in the frequency response function of the processing point, where the position of the machine tool processing point is characterized by the displacement (x, y, z) of the moving parts in all directions, and the spindle The rotational speed effect is characterized by quantitative gyro torque and centrifugal force; ② Define the machine tool as a machine tool form...
example 2
[0110] Taking a three-axis CNC machine tool as an example, the strokes of the moving parts in the x, y, and z directions of the machine tool are: 0 ~ 400 mm, 0 ~ 550 mm, 0 ~ 400 mm, and the range of the spindle speed n is 0 ~ 10000 rpm, feed per tooth f z The range of change is 0.03~0.3 mm / z, according to the diameter of 16mm and the number of teeth N Determine the cutting width a for an end mill of 4 e The range of variation is 0 ~ 16 mm, with the process parameter a e , f z , x, y, and z are variables, select 8 values from the value range of each variable as the 8 levels of the orthogonal experiment table in Table 1, and then combine the different levels of each variable to construct the orthogonal experiment table L64 (5 8 ), form the 64 sets of orthogonal test schemes shown in Table 2. Where Table 1 and Table 2 are as follows:
[0111] Table 1 Eight levels of the orthogonal experiment table
[0112]
[0113] Table 2 64 groups of orthogonal test schemes
[0114]...
PUM
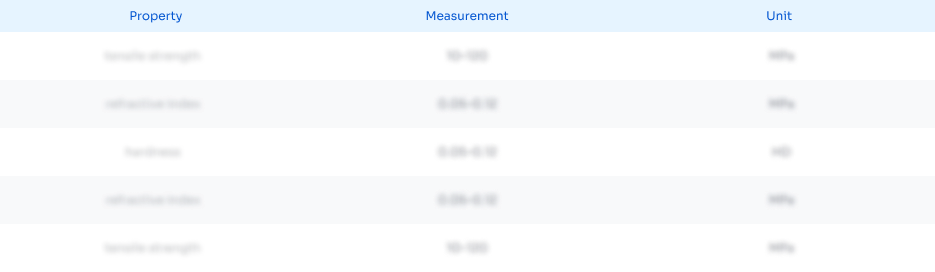
Abstract
Description
Claims
Application Information

- R&D
- Intellectual Property
- Life Sciences
- Materials
- Tech Scout
- Unparalleled Data Quality
- Higher Quality Content
- 60% Fewer Hallucinations
Browse by: Latest US Patents, China's latest patents, Technical Efficacy Thesaurus, Application Domain, Technology Topic, Popular Technical Reports.
© 2025 PatSnap. All rights reserved.Legal|Privacy policy|Modern Slavery Act Transparency Statement|Sitemap|About US| Contact US: help@patsnap.com