High-performance grouting material for connecting steel bar sleeve of fabricated bridge as well as use method and application of high-performance grouting material
A steel sleeve and assembly technology, applied in the direction of building components, structural elements, buildings, etc., can solve the problems of small strength increase, large shrinkage rate of sulphoaluminate, no research on low-temperature construction performance of grouting materials, etc., to achieve flow Good resistance, excellent compressive strength and rust resistance, low fluctuation effect
- Summary
- Abstract
- Description
- Claims
- Application Information
AI Technical Summary
Problems solved by technology
Method used
Image
Examples
Embodiment 1
[0074] Weigh 350kg 52.5 grade Portland cement, 85kg aluminate cement CA-50, 80kg microbeads, 60kg silica fume, 20kg mineral powder, 423kg sand, 6kg polycarboxylate comb polymer (molecular formula shown in formula I , where a is 75, b is 10, n is 80, R is CH 2 CH 2 , M is H), 0.5kg organosilicon defoamer, 0.5kg polyether defoamer, 0.08kg plastic expansion agent, 8kg calcium silicate hydrate powder, 6kg calcium nitrite, 10kg sodium nitrite, stir for 10min, After stirring evenly, the high-performance grouting material BG-1 for the steel bar sleeve connection of the prefabricated bridge is obtained. Weigh 10kg of BG-1, stir at a low speed for 30s, then add 1.03kg of water and continue to stir for 5min to obtain a grouting slurry.
Embodiment 2
[0076] Weigh 450kg 52.5 grade Portland cement, 30kg aluminate cement CA-50, 40kg microbeads, 20kg silica fume, 40kg mineral powder, 423kg sand, 5kg polycarboxylate comb polymer (molecular formula shown in formula I , where a is 65, b is 10, n is 90, R is CH 2 CH 2 , M is Na), 0.5kg silicone defoamer, 1kg polyether defoamer, 0.12kg plastic expansion agent, 4kg calcium silicate hydrate powder, 5kg calcium nitrite, 10kg sodium nitrite, stir for 10min, stir After uniformity, the high-performance grouting material BG-2 for the sleeve connection of prefabricated bridge steel bars was obtained. Weigh 10kg of BG-2, stir at a low speed for 30s, then add 0.94kg of water and continue stirring for 5min to obtain a grouting slurry.
Embodiment 3
[0078] Weigh 410kg 52.5 grade Portland cement, 60kg aluminate cement CA-50, 60kg microbeads, 20kg silica fume, 60kg mineral powder, 423kg sand, 4kg polycarboxylate comb-type polymer (molecular formula shown in formula I , where a is 50, b is 5, n is 70, R is CH 2 CH 2 CH 2 CH 2 , M is CH 2 CHCH 2 OH), 1kg organosilicon defoamer, 0.5kg polyether defoamer, 0.1kg plastic expansion agent, 5kg calcium silicate hydrate powder, 4kg calcium nitrite, 8kg sodium nitrite, stirred for 10min, and obtained after stirring evenly High-performance grouting material BG-3 for prefabricated bridge reinforcement sleeve connection. Weigh 10kg of BG-3, stir at a low speed for 25s, then add 1.1kg of water and continue stirring for 4min to obtain a grouting slurry.
PUM
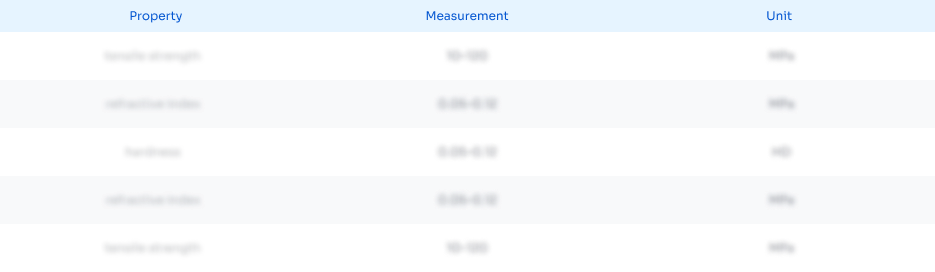
Abstract
Description
Claims
Application Information

- R&D
- Intellectual Property
- Life Sciences
- Materials
- Tech Scout
- Unparalleled Data Quality
- Higher Quality Content
- 60% Fewer Hallucinations
Browse by: Latest US Patents, China's latest patents, Technical Efficacy Thesaurus, Application Domain, Technology Topic, Popular Technical Reports.
© 2025 PatSnap. All rights reserved.Legal|Privacy policy|Modern Slavery Act Transparency Statement|Sitemap|About US| Contact US: help@patsnap.com