High-flame-retardant breathable protective fabric and preparation method thereof
A high flame retardant, fabric technology, applied in the field of textile fabrics, can solve the problem that protective fabrics cannot have both flame retardancy and air permeability, and achieve the effects of improving elasticity, preventing dripping or piercing, and improving shape retention.
- Summary
- Abstract
- Description
- Claims
- Application Information
AI Technical Summary
Problems solved by technology
Method used
Image
Examples
Embodiment 1
[0045] Phosphate monomers are made through the following steps:
[0046] D1. Add 0.11mol of pentaerythritol, 0.1mol of phosphorus oxychloride and 40mL of 1,4-dioxane into a three-necked flask equipped with mechanical stirring, thermometer, condensing reflux, drying and hydrogen chloride gas absorption devices, raise the temperature to 85°C, and stir Stop the reaction until no hydrogen chloride gas is generated, cool to room temperature, filter with suction, wash the precipitate twice with 1,4-dioxane and ethanol, and then dry in vacuum to constant weight to obtain caged phosphate;
[0047] D2. Add 0.21mol of caged phosphate, 100mL of acetonitrile, 3g of anhydrous aluminum trichloride and 0.35mol of triethylamine into a three-neck flask equipped with mechanical stirring, condensing reflux, temperature control, nitrogen protection and constant pressure dropping funnel , add 0.1mol allyl dimethyl chlorosilane, stir at 70 ° C for 1.5 h, then raise the temperature and reflux for 12...
Embodiment 2
[0049] Phosphate monomers are made through the following steps:
[0050] D1. Add 0.13mol of pentaerythritol, 0.1mol of phosphorus oxychloride and 60mL of 1,4-dioxane into a three-necked flask equipped with mechanical stirring, thermometer, condensing reflux, drying and hydrogen chloride gas absorption devices, and heat up to 85°C , stirred until no hydrogen chloride gas was generated, stopped the reaction, cooled to room temperature, filtered with suction, washed the precipitate twice with 1,4-dioxane and ethanol, and then dried in vacuum to constant weight to obtain caged phosphate;
[0051] D2. Add 0.25mol of caged phosphate, 200mL of acetonitrile, 5g of anhydrous aluminum trichloride and 0.55mol of triethylamine into a three-neck flask equipped with mechanical stirring, condensing reflux, temperature control, nitrogen protection and constant pressure dropping funnel , add 0.1mol allyl dimethyl chlorosilane, stir at 70 ° C for 1.5 h, then raise the temperature and reflux for...
Embodiment 3
[0053] Flame retardant polyester resin pellets are made through the following steps:
[0054] C1. After mixing 0.1mol hexafluorobutyl methacrylate, 0.1mol phosphoric ester monomer prepared in Example 1, 0.1mol 1,1,3,3-tetramethylsilane and anhydrous toluene, stir evenly, and then Under the protection of nitrogen, heat to 96 ° C, then add 1.35 g of chloroplatinic acid isopropanol solution, react for 5 hours, after the reaction, use activated carbon to adsorb the platinum catalyst, filter, and rotary evaporate to remove the solvent to obtain a flame retardant;
[0055] C2, 100g polyester granules, 15g flame retardant and 1.5g compatibilizer are added in the extruder, extruded and granulated to obtain flame retardant polyester resin pellets, wherein the rotating speed of the extruder is 200rpm, and the extrusion temperature The temperature is 160°C, the compatibilizer is maleic anhydride grafted polyethylene, and the polyester particles are PET particles.
PUM
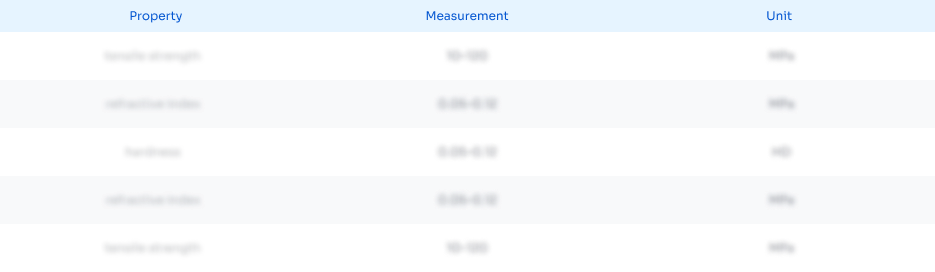
Abstract
Description
Claims
Application Information

- R&D
- Intellectual Property
- Life Sciences
- Materials
- Tech Scout
- Unparalleled Data Quality
- Higher Quality Content
- 60% Fewer Hallucinations
Browse by: Latest US Patents, China's latest patents, Technical Efficacy Thesaurus, Application Domain, Technology Topic, Popular Technical Reports.
© 2025 PatSnap. All rights reserved.Legal|Privacy policy|Modern Slavery Act Transparency Statement|Sitemap|About US| Contact US: help@patsnap.com