Binuclear vanadium catalyst as well as preparation method and application thereof
A technology of nuclear vanadium catalysts and uses, applied in the field of olefin polymerization organometallic catalysts and olefin coordination polymerization, can solve the problems of catalyst poisoning, loss of ability to catalyze olefin polymerization, etc., and achieve easy reaction, simple operation, and strong original innovation Effect
- Summary
- Abstract
- Description
- Claims
- Application Information
AI Technical Summary
Problems solved by technology
Method used
Image
Examples
Embodiment 1
[0042] Preparation of 2,6-dimethylvanadium trichloride: Under nitrogen atmosphere, take 2,6-dimethylphenylisocyanate (5.1g, 33.9mmol) into the Schlenk bottle, VOCl 3 (8.9g, 50.9mmol) was added to a Schlenk bottle, 15mL of n-octane was added, and the reaction was stirred and reacted at 135°C for 20 hours. During the reaction, gas was released every 15 minutes, and the system was in the form of a black-green solution at the end of the reaction. Filter with diatomaceous earth, rinse with dichloromethane, collect the filtrate, and dry in vacuo to obtain a purple-black powder solid, add a small amount of dichloromethane to dissolve, recrystallize with n-hexane, stand at -7°C for 24 hours, remove the solution, collect the solid, and vacuum After drying, 12.1 g of brown powder of 2,6-dimethylvanadium trichloride was obtained with a yield of 87%. The structural formula of 2,6-dimethylvanadium trichloride is as follows:
[0043]
[0044] figure 1 It is the NMR spectrum of 2,6-dime...
Embodiment 2
[0046] Preparation of binuclear vanadium complex: under nitrogen protection, weigh the 2,6-dimethylvanadium trichloride (200mg, 0.73mmol) prepared in Example 1 and dissolve it in toluene (10mL), and let stand at -29°C 1h; Weigh 4,4-dihydroxybiphenyl (67.9mg, 0.37mmol), add 4,4-dihydroxybiphenyl to trichloride in two batches, stir at room temperature for 12h, filter with diatomaceous earth, and obtain brown solution, the filtrate was vacuum removed to obtain the main catalyst Cat.1, its structure is as follows:
[0047]
[0048] figure 2 It is the NMR spectrum of cocatalyst Cat.1, which shows that the structure of the prepared catalyst is correct.
Embodiment 3
[0050] Ethylene polymerization: In an anhydrous and oxygen-free nitrogen glove box, take 1 μmol of the catalyst in a 10mL schleck bottle and add 8g of toluene; take 1500μmol of the cocatalyst diethylaluminum chloride and add it to another schleck bottle and add 6.5g of toluene, Make sure the total reaction volume is 20 mL. Take the two bottles out of the glove box, connect the double-row tube to replace the nitrogen, and then use them for later use. The polymerization reactor was dried at 100°C for 6 hours and then vacuumed for 3 hours. The kettle body was placed in an ice-water mixed bath until the temperature of the kettle body was maintained at 0°C for later use.
[0051] After the polymerization reaction device replaced the nitrogen three times, the nitrogen gas was kept flowing continuously, and 1500 μmol of the co-catalyst diethylaluminum chloride and the main catalyst Cat. Quickly open the ethylene valve, feed ethylene gas, discharge the nitrogen in the kettle through...
PUM
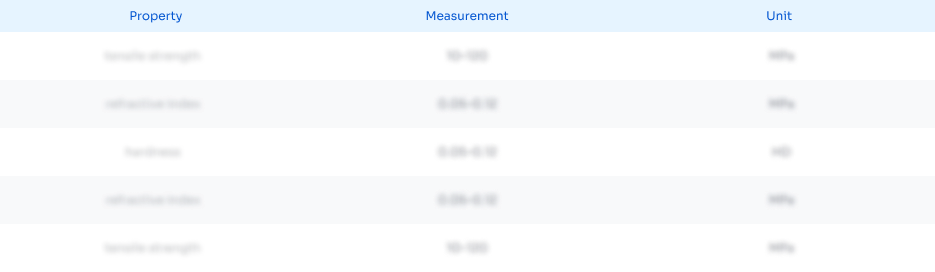
Abstract
Description
Claims
Application Information

- Generate Ideas
- Intellectual Property
- Life Sciences
- Materials
- Tech Scout
- Unparalleled Data Quality
- Higher Quality Content
- 60% Fewer Hallucinations
Browse by: Latest US Patents, China's latest patents, Technical Efficacy Thesaurus, Application Domain, Technology Topic, Popular Technical Reports.
© 2025 PatSnap. All rights reserved.Legal|Privacy policy|Modern Slavery Act Transparency Statement|Sitemap|About US| Contact US: help@patsnap.com