Copper electroplating formula for pulse through hole filling and electroplating process thereof
An electroplating process, a technology of electroplating copper, applied in the direction of the formation of electrical connections of printed components, etc., can solve the problems of low pulse electroplating process time, short plating ability and performance requirements, and many foams in surfactant components, so as to promote filling Hole and deep plating ability, reduced concentration polarization, excellent uniformity effect
- Summary
- Abstract
- Description
- Claims
- Application Information
AI Technical Summary
Problems solved by technology
Method used
Image
Examples
Embodiment 1
[0070] A formula for electroplating copper for pulse through-hole filling, calculated per liter of bath solution:
[0071] Copper sulfate 60g / L, concentrated sulfuric acid 150g / L, 2-butyl-1-octanol polyoxyethylene ether 30mg / L, thiodiglycol polyoxyethylene ether 10mg / L, sodium methylenedinesulfonate 1g / L, 1,4-dioxane 20mg / L, ethylene glycol tert-butyl ether 10mg / L, glyoxylic acid 10mg / L, polyethyleneimine 15mg / L, purple phenazine liquid polymer 15mg / L, The balance is pure water, the pH is 0.2, the operating temperature is 30°C, and the forward current density is 0.5A / dm 2 , reverse current density 2.0A / dm 2 , positive and negative pulse time ratio 10:1ms, time 50min.
[0072] In Example 1, by figure 1 According to the evaluation criteria, the test results are as follows: the average deep plating ability is 95.8%, the average hole filling ability is 96%, the hole is excellent, the hole is not broken, the hole is bright, there is no pothole, and there is no copper tumor.
Embodiment 2
[0074] A formula for electroplating copper for pulse through-hole filling, calculated per liter of bath solution:
[0075] Copper sulfate 75g / L, concentrated sulfuric acid 175g / L, 2-butyl-1-octanol polyoxyethylene ether 60mg / L, thiodiglycol polyoxyethylene ether 20mg / L, sodium methylene di-naphthalene sulfonate 4.5 g / L, 1,4-dioxane 10mg / L, ethylene glycol tert-butyl ether 5mg / L, glyoxylic acid 5mg / L, polyethyleneimine 30mg / L, purple phenazine liquid polymer 30mg / L , the balance is pure water, the pH is 0.2, the operating temperature is 30°C, and the forward current density is 0.5A / dm 2 , reverse current density 2.0A / dm 2 , positive and negative pulse time ratio 10:1ms, time 50min.
[0076] In Example 2, by figure 1 According to the evaluation criteria, the test results are as follows: the average deep plating ability is 95.8%, the average hole filling ability is 96%, the hole is excellent, the hole is not broken, the hole is bright, there is no pothole, and there is no copp...
Embodiment 3
[0078] A formula for electroplating copper for pulse through-hole filling, calculated per liter of bath solution:
[0079] Copper sulfate 90g / L, concentrated sulfuric acid 200g / L, 2-butyl-1-octanol polyoxyethylene ether 90mg / L, thiodiglycol polyoxyethylene ether 30mg / L, sodium methylenedinesulfonate 8g / L, 1,4-dioxane 30mg / L, ethylene glycol tert-butyl ether 15mg / L, glyoxylic acid 15mg / L, polyethyleneimine 45mg / L, purple phenazine liquid polymer 45mg / L, The balance is pure water, the pH is 0.2, the operating temperature is 30°C, and the forward current density is 0.5A / dm 2 , reverse current density 2.0A / dm 2 , positive and negative pulse time ratio 10:1ms, time 50min.
[0080] In Example 3, by figure 1 According to the evaluation criteria, the test results are as follows: the average deep plating ability is 95.8%, the average hole filling ability is 96%, the hole is excellent, the hole is not broken, the hole is bright, there is no pothole, and there is no copper tumor.
PUM
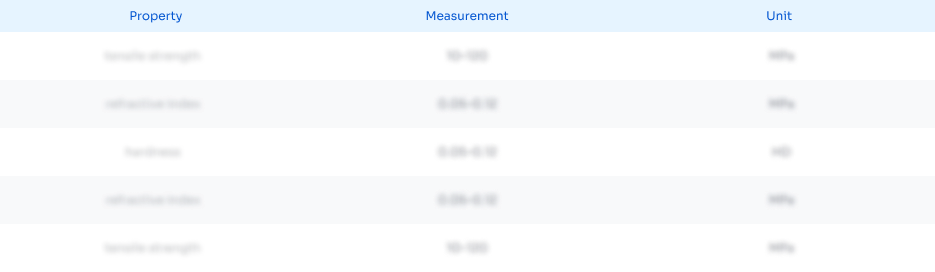
Abstract
Description
Claims
Application Information

- Generate Ideas
- Intellectual Property
- Life Sciences
- Materials
- Tech Scout
- Unparalleled Data Quality
- Higher Quality Content
- 60% Fewer Hallucinations
Browse by: Latest US Patents, China's latest patents, Technical Efficacy Thesaurus, Application Domain, Technology Topic, Popular Technical Reports.
© 2025 PatSnap. All rights reserved.Legal|Privacy policy|Modern Slavery Act Transparency Statement|Sitemap|About US| Contact US: help@patsnap.com