Production process of safe and low-waste tetrabromoethane
A tetrabromoethane and production process technology, applied in the field of safe and low-waste tetrabromoethane production process, can solve the problems of low reaction efficiency, side reactions, consumption, etc., reduce reaction by-products, avoid the use of water, The effect of shortening the reaction time
- Summary
- Abstract
- Description
- Claims
- Application Information
AI Technical Summary
Problems solved by technology
Method used
Image
Examples
Embodiment 1
[0029] The preparation of amino tertiary amine compound:
[0030] B1. Under the condition of ice-water bath, add 0.1mol methylamine and 15mL methanol into the reaction vessel, stir evenly, then slowly add 0.2mol acrylonitrile dropwise under stirring, the drop rate is 1 drop / 3 seconds, remove the ice-water bath after the drop is complete , warmed up to room temperature, stirred for 4h, and the solvent was removed by rotary evaporation to obtain intermediate 1;
[0031] B2. Put 20g of intermediate 1, 100mL of methanol, 0.15g of sodium hydroxide and 4g of W-3 type Raney nickel catalyst into the autoclave, replace it with nitrogen for 3 times and hydrogen for 3 times, then at 90°C, 2.0MPa Under the conditions, stir at a speed of 500r / min until the hydrogen pressure no longer decreases, and continue to stir for 6h, filter the reaction solution and remove the solvent by rotary evaporation to obtain an amino tertiary amine compound.
Embodiment 2
[0033] Preparation of modified separation membrane:
[0034] A1. Put 10g of mesoporous molecular sieves in a four-neck flask, heat up to 200°C, heat for 3 hours, and continue vacuuming; after cooling to room temperature, pour 100mL of n-heptane into the reaction flask, stir, condense and reflux, and heat To 80°C, add 2g of 1,1,3,3-tetramethyldisilazane dropwise, react for 8 hours, let stand after cooling, wash repeatedly with n-heptane, and dry at 50°C to obtain a modified mesoporous molecular sieve;
[0035] A2. Add 0.1mol 3-glycidyl etheroxypropyltrimethoxysilane, 0.11mol amino tertiary amine compound, 0.2mol triethylamine and 120mL n-heptane into a four-necked flask, stir for 6 hours, filter, and remove the liquid Rotary steaming under pressure to obtain modified siloxane;
[0036] A3. Add 20g of modified siloxane to n-heptane solution containing 100g of polydimethylsiloxane, stir for 10min, then add 12g of modified mesoporous molecular sieve, ultrasonicate for 25min, and ...
Embodiment 3
[0038] Preparation of modified separation membrane:
[0039] A1. Put 10g of mesoporous molecular sieves in a four-neck flask, heat up to 200°C, heat for 3h, and continue vacuuming; after cooling to room temperature, pour 100mL of n-heptane into the reaction flask, condense and reflux, and heat to 80 ℃, then add 4g of 1,1,3,3-tetramethyldisilazane dropwise, react for 8h, let stand after cooling, wash repeatedly with n-heptane, and dry at 50℃ to obtain a modified mesoporous molecular sieve;
[0040] A2. Add 0.1mol 3-glycidyl etheroxypropyl trimethoxysilane, 0.13mol amino tertiary amine compound, 0.2mol triethylamine and 150mL n-heptane into a four-necked flask, stir for 6 hours, filter, and depressurize the liquid Rotary steaming to obtain modified siloxane;
[0041] A3. Add 35g of modified siloxane to n-heptane solution containing 100g of polydimethylsiloxane, stir for 20min, then add 22g of modified mesoporous molecular sieve, ultrasonicate for 40min, and finally add 2.5g of n-...
PUM
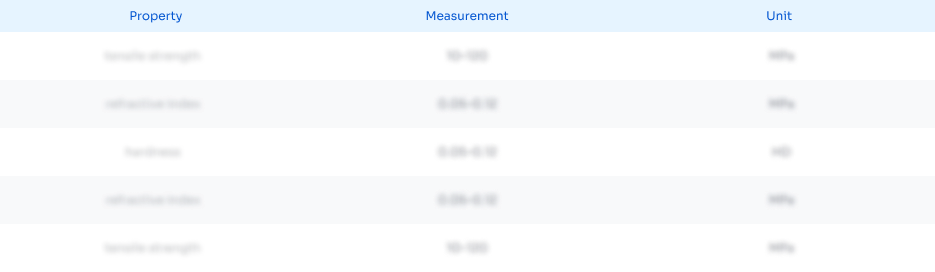
Abstract
Description
Claims
Application Information

- R&D
- Intellectual Property
- Life Sciences
- Materials
- Tech Scout
- Unparalleled Data Quality
- Higher Quality Content
- 60% Fewer Hallucinations
Browse by: Latest US Patents, China's latest patents, Technical Efficacy Thesaurus, Application Domain, Technology Topic, Popular Technical Reports.
© 2025 PatSnap. All rights reserved.Legal|Privacy policy|Modern Slavery Act Transparency Statement|Sitemap|About US| Contact US: help@patsnap.com