Continuous production of methylpentenone using cation exchange resin in fixed bed reactor
A technology of methyl pentenone and reactor, applied in the direction of cation exchange, ion exchange, ion exchange column/bed method, etc.
- Summary
- Abstract
- Description
- Claims
- Application Information
AI Technical Summary
Problems solved by technology
Method used
Image
Examples
Embodiment 1
[0093] A stainless steel fixed bed reactor SS-316 (length 470 cm, inner diameter 5.08 cm) was used for the reaction. The reactor was charged with catalyst Amberlyst-15 (3.15 kg). MEK was fed into the reactor using a pump at a rate of 8.67 gm / min in the main line. Such as figure 2 Acetaldehyde was fed to the column through 6 side injection ports at 0.9 gm / min (MEK 55.56% (w / w)) as indicated. Experiments were carried out at 363-368K and 5 barg with a total feed ratio of 1:3 (AcH:MEK) with a total feed flow rate of 18 kg / day to 18.5 kg / day (295 min residence time). The reactor is heated using electrical coils wrapped around the reactor column. The experiment was carried out continuously for 300 hours. It was found that the MPO yield varied from 75% to 80% (based on acetaldehyde) within 300 hours at an average feed molar ratio close to 1:3 (AcH:MEK). The MPO yield was verified by distillation. This result is very important because it demonstrates the broad application of Am...
Embodiment 2
[0096] A stainless steel fixed bed reactor SS-316 (length 470 cm, inner diameter 5.08 cm) was used for the reaction. The reactor was charged with catalyst Amberlyst-15 (3.15 kg). MEK was fed into the reactor using a pump at a rate of 8.67 gm / min in the main line. Such as figure 2 Acetaldehyde was fed into the column at 0.71 gm / min (MEK 55.56% (w / w)) through 6 side injection ports as indicated. Experiments were carried out at 363-368K and 5 barg with a total feed ratio of 1:3.5 (AcH:MEK) with a total feed flow rate of 18 kg / day to 18.5 kg / day (345 min residence time). The reactor is heated using electrical coils wrapped around the reactor column. The experiment was carried out continuously for 300 hours. MPO yields were found to vary in the range of 80% to 85% (based on acetaldehyde). The MPO yield was verified by actual distillation. This result is very important because it demonstrates the broad application of Amberlyst-15 in the production of methylpentenone on an ind...
Embodiment 4A
[0109] Example 4A: The experiment was carried out in a SS-316 batch reactor at 343K for 6 hours using 100 g of pure methyl ethyl ketone (MEK) and 10 g of Amberlyst-15. The loss of MEK due to the aldol reaction was only 4% to 5% due to the formation of 4gm to 5gm of 5-methyl-4-hepten-3-one as seen from GC-FID. The volume of the batch reactor used in the reaction was 250 ml, in which 125 ml of MEK was used.
PUM
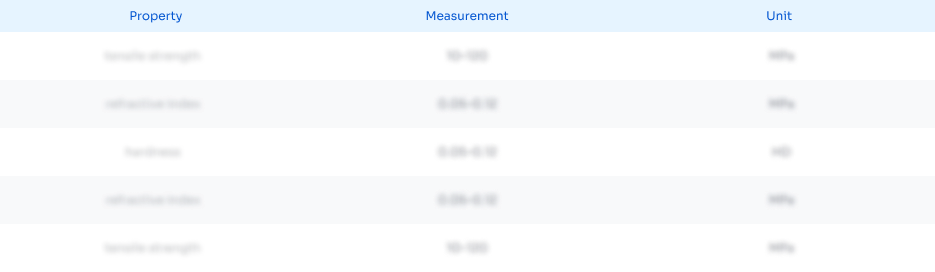
Abstract
Description
Claims
Application Information

- R&D Engineer
- R&D Manager
- IP Professional
- Industry Leading Data Capabilities
- Powerful AI technology
- Patent DNA Extraction
Browse by: Latest US Patents, China's latest patents, Technical Efficacy Thesaurus, Application Domain, Technology Topic, Popular Technical Reports.
© 2024 PatSnap. All rights reserved.Legal|Privacy policy|Modern Slavery Act Transparency Statement|Sitemap|About US| Contact US: help@patsnap.com