A Fatigue Life Prediction Method Based on Fatigue Crack Growth
A technology for fatigue life prediction and fatigue crack growth, which is applied in the testing of mechanical components, testing of machine/structural components, and measuring devices. Accurate prediction of appearance and other issues, to achieve the effect of simplifying the analysis process, reducing computing costs, and improving computing efficiency
- Summary
- Abstract
- Description
- Claims
- Application Information
AI Technical Summary
Problems solved by technology
Method used
Image
Examples
Embodiment 1
[0100] Figure 1
[0101] S1: Global Model Modeling
[0106] S2: Hydrodynamic Analysis
[0108] S21: The wave environment refers to a series of regular waves that define potential flow theoretical analysis, including wave direction, wave frequency, and working
[0111] S31: overall model strength analysis
[0113] S32: local intensity analysis
[0118] S324 calls the structural strength solver to carry out calculation analysis, and the result is shown in Figure 11.
[0125] S45 Finite Element Analysis (Trial): Run the reorganized submodel in ABAQUS to determine the Mises in the crack propagation zone
[0127] The crack insertion and mesh update process can be shown in FIG. 9 .
[0131] According to the inserted cracks (including initial cracks and cracks inserted during crack propagation)
[0134] The fatigue performance under the current crack size and operating conditions is characterized by the stress intensity factor transfer function. traverse
[0139]
[0141]
[0144]
[014...
Embodiment 2
PUM
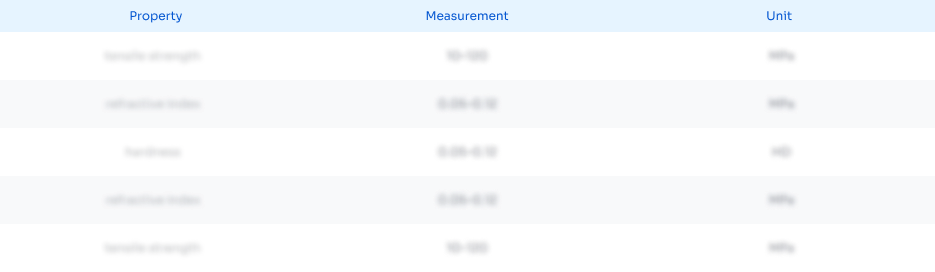
Abstract
Description
Claims
Application Information

- R&D
- Intellectual Property
- Life Sciences
- Materials
- Tech Scout
- Unparalleled Data Quality
- Higher Quality Content
- 60% Fewer Hallucinations
Browse by: Latest US Patents, China's latest patents, Technical Efficacy Thesaurus, Application Domain, Technology Topic, Popular Technical Reports.
© 2025 PatSnap. All rights reserved.Legal|Privacy policy|Modern Slavery Act Transparency Statement|Sitemap|About US| Contact US: help@patsnap.com