Forging and heat treatment method for martensite heat-resistant stainless steel special-shaped forge piece
A technology of heat-resistant stainless steel and heat treatment methods, applied in heat treatment furnaces, heat treatment equipment, furnace types, etc., can solve problems such as difficulty in meeting final performance requirements, complex production process, and many forging fires, and achieve grain size refinement, Effect of improving composition segregation and lowering forging temperature
- Summary
- Abstract
- Description
- Claims
- Application Information
AI Technical Summary
Problems solved by technology
Method used
Image
Examples
Embodiment 1
[0044] A method for forging and heat treating a martensitic heat-resistant stainless steel special-shaped forging, comprising the following steps:
[0045] The raw materials are smelted, and the smelting process is the process of EF+LF+VD+Electroslag on the raw materials.
[0046] After the smelting treatment, the raw materials are heated in a natural gas furnace. After the heating parameter in the natural gas furnace is 600°C for 2 hours, the temperature is raised to 800°C for 3 hours, and then the temperature is raised to 1190°C for 5 hours. After heating, carry out forging with five fires:
[0047] The first fire: thicken the billet, and hold the temperature at 1190°C for 2.5 hours after forging.
[0048] The second fire: Punch the billet with a punch, and keep the temperature at 1190°C for 2 hours after forging.
[0049] The third fire time: the billet is reamed with a horse rod, and the heat preservation temperature is 1190°C for 1.5 hours after forging.
[0050] The fou...
Embodiment 2
[0058] A method for forging and heat treating a martensitic heat-resistant stainless steel special-shaped forging, comprising the following steps:
[0059] The raw materials are smelted, and the smelting process is the process of electric furnace + LF + VD + ESR for raw materials.
[0060] After the smelting treatment, the raw materials are heated in a natural gas furnace. After the heating parameter in the natural gas furnace is 600°C for 2.5 hours, the temperature is raised to 750°C for 4 hours, and then the temperature is raised to 1230°C for 4 hours. After heating, carry out forging with five fires:
[0061] The first fire: thicken the billet, and hold the temperature at 1190°C for 2.5 hours after forging.
[0062] The second firing: the billet is punched through the hole with a punch, and the heat preservation temperature is 1190°C for 2 hours after forging.
[0063] The third fire time: the billet is reamed with a horse rod, and the heat preservation temperature is 119...
Embodiment 3
[0072] A method for forging and heat treating a martensitic heat-resistant stainless steel special-shaped forging, comprising the following steps:
[0073] The raw materials are smelted, and the smelting process is the process of EF+LF+VD+Electroslag on the raw materials.
[0074] After the smelting treatment, the raw materials are heated in a natural gas furnace. After the heating parameter in the natural gas furnace is 600°C for 1.5 hours, the temperature is raised to 850°C for 2 hours, and then the temperature is raised to 1150°C for 6 hours. After heating, carry out forging with five fires:
[0075] The first fire: thicken the billet, and hold the temperature at 1190°C for 2.5 hours after forging.
[0076] The second firing: the billet is punched through the hole with a punch, and the heat preservation temperature is 1190°C for 2 hours after forging.
[0077] The third fire time: the billet is reamed with a horse rod, and the heat preservation temperature is 1190°C for 1...
PUM
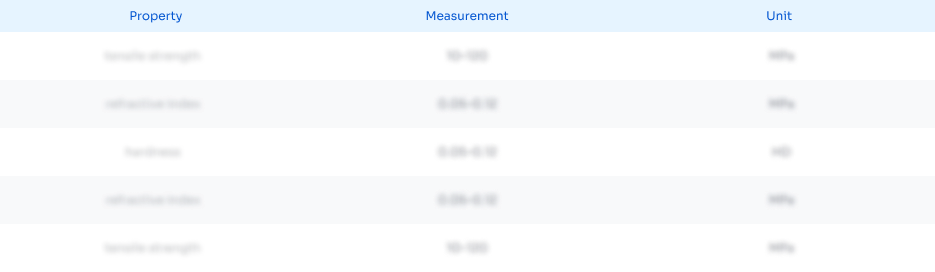
Abstract
Description
Claims
Application Information

- R&D Engineer
- R&D Manager
- IP Professional
- Industry Leading Data Capabilities
- Powerful AI technology
- Patent DNA Extraction
Browse by: Latest US Patents, China's latest patents, Technical Efficacy Thesaurus, Application Domain, Technology Topic, Popular Technical Reports.
© 2024 PatSnap. All rights reserved.Legal|Privacy policy|Modern Slavery Act Transparency Statement|Sitemap|About US| Contact US: help@patsnap.com