Plastic package material of AC permanent magnet submersible motor, plastic package technique and application
A technology of submersible motors and plastic packaging materials, which is applied in the manufacture of motor generators, electromechanical devices, electrical components, etc., can solve the problems of insufficient potting on the inner wall of the stator, unsatisfactory actual effect, and complicated plastic packaging process, so as to improve the yield rate and Insulation reliability, improved plastic sealing efficiency, and good fluidity
- Summary
- Abstract
- Description
- Claims
- Application Information
AI Technical Summary
Problems solved by technology
Method used
Image
Examples
Embodiment 1
[0048] The stator and the rotor structure of the AC permanent magnet submersible motor prepared by the present invention are respectively as shown in Figure 1 and Figure 2, as can be seen from Figure 1, the stator is a concentrated winding structure, including a stator casing 1, a stator winding 1'; Iron core 1", the stator casing 1 is connected with the stator winding and the iron core by potting the plastic sealing material 2 inside it to form an integrated structure; the stator winding and the iron core in the potting body are not eroded by the external liquid; The potting is characterized in that: the inner circumference and both ends of the stator are filled with plastic sealing material 2, and form an integral stator with the stator core and stator windings inside the stator casing 1. As can be seen from Figure 2, the rotor includes non- Magnetic anti-corrosion jacket 4, cage-type starting winding 5, permanent magnet 6, rotor yoke 7, rotor shaft 7', the rotor yoke 7, perm...
Embodiment 2
[0054] This embodiment is the same as Embodiment 1 except for the following features: the plastic sealing structure of the stator is shown in Figure 3, and the plastic sealing material is composed of four materials: 6101 epoxy resin, 6630 thinner, H230 curing toughening agent, and silicon micropowder. Its weight ratio is 80:20:30:150; the specific preparation process is: first add 6101 epoxy resin 80 (weight ratio, the same below) to the batching container, then add 6630 diluent 20 for stirring, stir well and then add The microsilica powder 150 is stirred evenly again, and finally the H230 solidified toughening agent 30 is added and stirred evenly for use. Clean the stator to be potted and put it into the potting mold. The potting and curing process is as follows——
[0055] Potting: put the motor stator 9 that has been loaded into the lower mold 10 of the potting mold into a 70°C oven and heat it for 0.5 hours, take it out, and slowly inject the prepared potting material 2 int...
Embodiment 3
[0058] This embodiment is the same as Embodiment 1 except for the following features: the plastic sealing structure of the stator is shown in Figure 3, and the plastic sealing material is composed of four materials: 6101 epoxy resin, 6630 thinner, H230 curing toughening agent, and silicon micropowder. Its weight ratio is 70:23:25:135; the specific preparation process is: first add 6101 epoxy resin 70 (weight ratio, the same below) to the batching container, then add 6630 diluent 23 for stirring, stir well and then add The microsilica powder 135 is stirred evenly again, and finally the H230 curing toughening agent 25 is added and stirred evenly for use. Clean the stator to be potted and put it into the potting mold. The potting and curing process is as follows——
[0059] Potting: put the motor stator 9 that has been loaded into the lower mold 10 of the potting mold into a 70°C oven and heat it for 0.5 hours, take it out, and slowly inject the prepared potting material 2 into th...
PUM
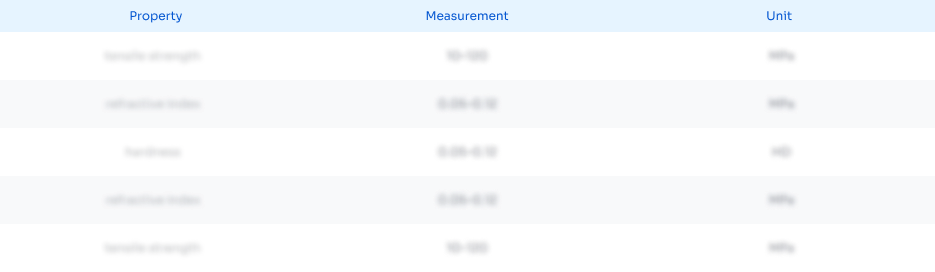
Abstract
Description
Claims
Application Information

- R&D
- Intellectual Property
- Life Sciences
- Materials
- Tech Scout
- Unparalleled Data Quality
- Higher Quality Content
- 60% Fewer Hallucinations
Browse by: Latest US Patents, China's latest patents, Technical Efficacy Thesaurus, Application Domain, Technology Topic, Popular Technical Reports.
© 2025 PatSnap. All rights reserved.Legal|Privacy policy|Modern Slavery Act Transparency Statement|Sitemap|About US| Contact US: help@patsnap.com