Tin-plated copper alloy conductor production process and tin-plated structure
A conductor production, tinned copper technology, applied in hot-dip plating process, metal material coating process, coating, etc., can solve the economic loss of enterprises, inconvenient soft wire, affecting the solderability of wires and signal transmission, etc. , to achieve the effect of reheating and reuse
- Summary
- Abstract
- Description
- Claims
- Application Information
AI Technical Summary
Problems solved by technology
Method used
Image
Examples
Embodiment 1
[0039] A tinned copper alloy conductor production process, the specific steps are as follows:
[0040] Step 1, the grinding machine removes the surface oxide of the copper-aluminum rare-earth alloy billet, and obtains the copper-aluminum rare-earth alloy ingot;
[0041] Step 2: Stretch the aluminum alloy ingot with a water tank-type drawing machine, spray drawing oil synchronously during stretching, and the drawing speed is 400m / min, and obtain a busbar with a wire diameter of 2.05mm;
[0042] Step 3, the wire drawing machine draws the bus bar to obtain wire rods, and the diameter of the wire rods is 0.8mm;
[0043]Step 4. Put the wire rod in a heating furnace for softening treatment. The temperature of the heating furnace is controlled at 490°C. The heating furnace is combined with steam for anti-oxidation isolation. The softening speed is 200m / min to obtain soft wire;
[0044] Step 5. The soft wire is transported to the tinning machine, and the tinning machine evenly smears...
Embodiment 2
[0047] A tinned copper alloy conductor production process, the specific steps are as follows:
[0048] Step 1, the grinding machine removes the surface oxide of the copper-aluminum rare-earth alloy billet, and obtains the copper-aluminum rare-earth alloy ingot;
[0049] Step 2: Stretch the aluminum alloy ingot with a water tank-type drawing machine, spray drawing oil synchronously during stretching, and the drawing speed is 400m / min, and obtain a busbar with a wire diameter of 2.05mm;
[0050] Step 3, the wire drawing machine draws the bus bar to obtain wire rods, and the diameter of the wire rods is 0.8mm;
[0051] Step 4. Put the wire rod in a heating furnace for softening treatment. The temperature of the heating furnace is controlled at 510°C. The heating furnace is combined with steam for anti-oxidation isolation. The softening speed is 200m / min to obtain soft wire;
[0052] Step 5. The soft wire is transported to the tinning machine, and the tinning machine evenly smear...
Embodiment 3
[0056] Embodiment 3 is a further improvement to Embodiment 1.
[0057] Such as Figure 1-7 As shown, a tin-plating structure of a tin-plated copper alloy conductor production process, the tin-plating structure is the tinning machine in step five, the tin-plating structure includes a box body 1, and a V-shaped liquid collecting plate 5 is fixedly connected in the box body 1 The left and right ends of the top of the box body 1 are respectively connected with an outgoing wire guide structure 2 and an incoming wire guide structure 7 for guiding wires. The outgoing wire guide structure 2 and the incoming wire guide structure 7 have the same structure. The outgoing wire guide structure 2 includes guide rollers 21, rotating The shaft 22 and the rotating shaft 22, the supporting plate 23 are installed on the top of the box body 1, the inner wall of the supporting plate 23 is connected with the rotating shaft 22 through the bearing rotation, and the guiding roller 21 is evenly and fixe...
PUM
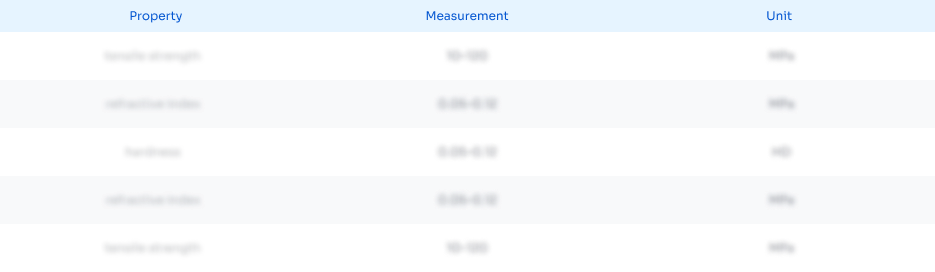
Abstract
Description
Claims
Application Information

- R&D Engineer
- R&D Manager
- IP Professional
- Industry Leading Data Capabilities
- Powerful AI technology
- Patent DNA Extraction
Browse by: Latest US Patents, China's latest patents, Technical Efficacy Thesaurus, Application Domain, Technology Topic, Popular Technical Reports.
© 2024 PatSnap. All rights reserved.Legal|Privacy policy|Modern Slavery Act Transparency Statement|Sitemap|About US| Contact US: help@patsnap.com