Cross beam structure strain change rate damage identification method and system
A technology of strain change rate and damage identification, applied in neural learning methods, neural architecture, design optimization/simulation, etc., can solve problems such as inability to quickly identify damage, achieve high engineering application value, strong anti-electromagnetic interference ability, and improve accuracy sexual effect
- Summary
- Abstract
- Description
- Claims
- Application Information
AI Technical Summary
Problems solved by technology
Method used
Image
Examples
Embodiment 1
[0043] refer to figure 1 , the present embodiment provides a strain change rate damage identification method for a beam structure, which specifically includes the following steps:
[0044] S101: Discretize the beam structure, and perform virtual layout of the FBG sensor network based on the finite element model.
[0045] The beam structure is discretized based on the quadrilateral four-node inverse shell element shown in Fig. 2(a).
[0046] Among them, the quadrilateral four-node inverse shell element (IQS4) is constructed based on the Mindlin plate deformation theory.
[0047]Specifically, each node of the quadrilateral four-node inverse shell element has 6 displacement degrees of freedom, including three translational degrees of freedom and three rotational degrees of freedom along the X-axis, Y-axis and Z-axis of the Cartesian coordinate system, as Figure 2(b) shows. The thickness of the quadrilateral four-node inverse shell element is 2t, and the displacement mode of th...
Embodiment 2
[0104] This embodiment provides a strain change rate damage identification system for a beam structure, which specifically includes the following modules:
[0105] A virtual layout module, which is used to discretize the beam structure, and perform virtual layout of the FBG sensor network based on the finite element model;
[0106] Displacement reconstruction module, which is used to calculate structural analysis strain based on FBG sensor network virtual layout and weighted least squares function of inverse finite element method, and then perform displacement reconstruction combined with boundary conditions;
[0107] Layout optimization module, which is used to judge whether the FBG sensor layout needs to be optimized according to the reconstruction error, if so, optimize the FBG sensor layout and paste it to the actual beam structure; otherwise, directly lay out the FBG sensor network virtual layout to the actual beam structure structurally;
[0108] Strain change rate calc...
Embodiment 3
[0112] This embodiment provides a computer-readable storage medium, on which a computer program is stored, and when the program is executed by a processor, the steps in the method for identifying the strain change rate damage of the beam structure as described above are implemented.
PUM
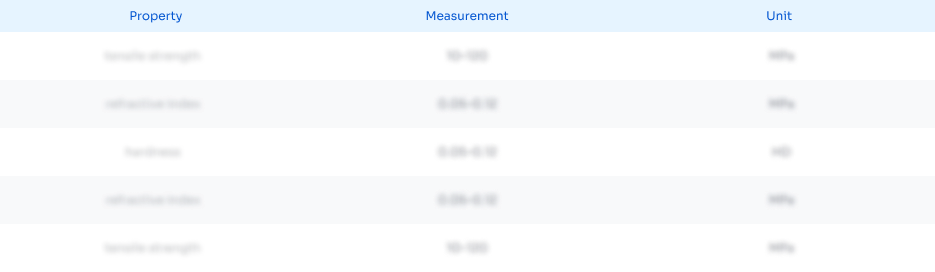
Abstract
Description
Claims
Application Information

- Generate Ideas
- Intellectual Property
- Life Sciences
- Materials
- Tech Scout
- Unparalleled Data Quality
- Higher Quality Content
- 60% Fewer Hallucinations
Browse by: Latest US Patents, China's latest patents, Technical Efficacy Thesaurus, Application Domain, Technology Topic, Popular Technical Reports.
© 2025 PatSnap. All rights reserved.Legal|Privacy policy|Modern Slavery Act Transparency Statement|Sitemap|About US| Contact US: help@patsnap.com