Wood nanocellulose modified cemented filling material for deep ground structure filling and preparation method of wood nanocellulose modified cemented filling material
A technology for cementing filling materials and nanocellulose, which is applied in the field of mine filling materials, and can solve the problems that the underground space of goaf is difficult to reuse, and the solid waste of mines cannot meet the needs of filling.
- Summary
- Abstract
- Description
- Claims
- Application Information
AI Technical Summary
Problems solved by technology
Method used
Image
Examples
Embodiment 1
[0045] Preparation of lignocellulosic modified cemented filling materials:
[0046] (1) Add 0.5kg of crushed waste wood to 10kg of citric acid-sodium citrate buffer solution with pH5.0, soak for 24h, add 5g of xylanase, heat to 50°C, enzymatically hydrolyze for 1.5h, cool Finally, add 0.25kg cationic styrene-acrylic emulsion, transfer to the ball milling device and carry out ball milling (the ball-to-material ratio is 20:1), the ball milling speed is 2000rpm, and the ball milling time is 6h, after the end, obtain the lignonanocellulose modified by cationic styrene-acrylic emulsion solution;
[0047] (2) Take 40 g of the modified lignonanocellulose solution prepared in step (1), add 4 kg of water to dilute, pour a part of the diluted solution into 12 kg of coal gangue, add to just submerged coal gangue, soak for 12 hours, and leave the rest Mix the diluent with 3kg of cement, 1.5kg of fly ash, and 5kg of tailings, mix all the materials after stirring for 10 minutes, and contin...
Embodiment 2
[0049] Preparation of lignocellulosic modified cemented filling materials:
[0050] (1) Add 0.5kg of crushed waste wood to 10kg of pH4.0 citric acid-sodium citrate buffer solution, soak for 18h, add 5g of xylanase, heat to 45°C, enzymatically hydrolyze for 1.5h, cool Finally, add 0.25kg cationic styrene-acrylic emulsion, transfer to ball milling device and carry out ball milling (ball-to-material ratio is 20:1), ball milling speed is 2200rpm, and ball milling time is 5.5h, obtains the wood nanofiber modified by cationic styrene-acrylic emulsion after finishing prime solution;
[0051] (2) Get 50 g of the modified lignonanocellulose solution prepared in step (1), add 4.5 kg of water to dilute, pour a part of the diluted solution into 10 kg of coal gangue, add to just submerged coal gangue, soak for 14 hours, The remaining dilution was mixed with 4.5kg cement, 1.0kg fly ash, and 5.5kg tailings, and after stirring for 10 minutes, all the materials were mixed, and the stirring wa...
Embodiment 3
[0053] Preparation of lignocellulosic modified cemented filling materials:
[0054] (1) Add 0.5kg of crushed waste wood to 10kg of pH4.5 citric acid-sodium citrate buffer solution, soak for 12h, add 5g of xylanase, heat to 55°C, enzymatically hydrolyze for 2h, after cooling Add 0.25kg of cationic styrene-acrylic emulsion, transfer to ball milling device and carry out ball milling (ball-to-material ratio is 20:1), ball milling speed is 2500rpm, ball milling time is 5h, after the end, obtain the lignonanocellulose solution modified by cationic styrene-acrylic emulsion ;
[0055] (2) Get 60g of the modified lignonanocellulose solution prepared by step (1), add 4.2kg of water to dilute, pour a part of the diluted solution into 11kg of coal gangue, add to just submerged coal gangue, soak for 16h, The remaining diluted solution was mixed with 4kg of cement, 1.5kg of fly ash, and 5.5kg of tailing sand. After stirring for 10 minutes, all the materials were mixed, and the stirring was...
PUM
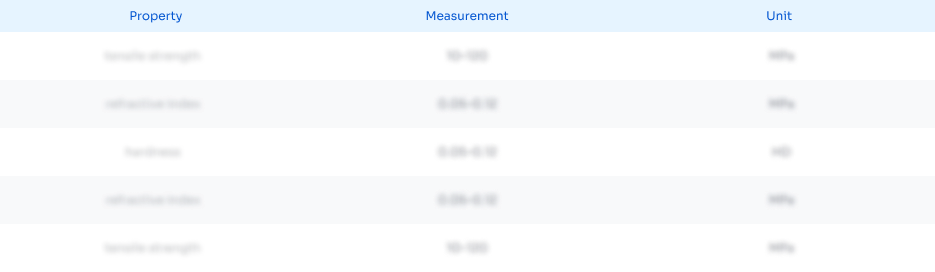
Abstract
Description
Claims
Application Information

- R&D Engineer
- R&D Manager
- IP Professional
- Industry Leading Data Capabilities
- Powerful AI technology
- Patent DNA Extraction
Browse by: Latest US Patents, China's latest patents, Technical Efficacy Thesaurus, Application Domain, Technology Topic, Popular Technical Reports.
© 2024 PatSnap. All rights reserved.Legal|Privacy policy|Modern Slavery Act Transparency Statement|Sitemap|About US| Contact US: help@patsnap.com