Processing technology of a metal-ceramic tool
A metal-ceramic and processing technology, applied in the field of tool manufacturing, can solve the problems of poor manufacturing precision of metal-ceramic tools, and achieve the effects of reducing drill bit collapse, improving processing accuracy and facilitating operation
- Summary
- Abstract
- Description
- Claims
- Application Information
AI Technical Summary
Problems solved by technology
Method used
Image
Examples
Embodiment Construction
[0052] Attached to the following Figure 1-9 This application will be described in further detail.
[0053] The embodiment of the present application discloses a processing technology of a cermet tool. refer to figure 1 , a processing technology of a cermet tool includes the following process steps:
[0054] S1. Pre-compression molding: pre-compress the powdery raw materials;
[0055] S2, low temperature treatment: perform low temperature treatment on the powdery raw materials pre-pressed in S1;
[0056] S3, hot pressing vibration sintering: the raw material obtained in S2 is subjected to pressure heating and sintering;
[0057] S4. Grinding: Grinding the sintered raw material to obtain a cermet tool blank;
[0058] S5, quenching: salt bath quenching of the cermet tool blank;
[0059] S6. Tempering: Temper the quenched cermet tool blank;
[0060] S7, fine grinding prototype: fine grinding the two ends and contours of the cermet tool blank, to obtain a semi-finished cerm...
PUM
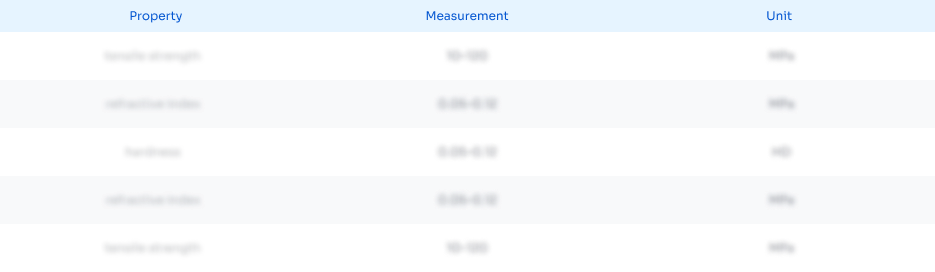
Abstract
Description
Claims
Application Information

- R&D
- Intellectual Property
- Life Sciences
- Materials
- Tech Scout
- Unparalleled Data Quality
- Higher Quality Content
- 60% Fewer Hallucinations
Browse by: Latest US Patents, China's latest patents, Technical Efficacy Thesaurus, Application Domain, Technology Topic, Popular Technical Reports.
© 2025 PatSnap. All rights reserved.Legal|Privacy policy|Modern Slavery Act Transparency Statement|Sitemap|About US| Contact US: help@patsnap.com