Reinforcing method of continuous carbon fiber toughened ceramic matrix composite material
A technology of toughening ceramics and composite materials, applied in the field of ceramic composite materials, can solve problems such as development time, cost waste, shedding failure, repair failure, etc., achieve a wide range of use environments, improve repair reliability, and improve performance.
- Summary
- Abstract
- Description
- Claims
- Application Information
AI Technical Summary
Problems solved by technology
Method used
Examples
Embodiment 1
[0041] This embodiment provides a continuous carbon fiber reinforced ceramic matrix composite reinforcement method, the specific process is as follows:
[0042] 1. Use ethanol to clean the new acupuncture structure C / SiC component body, including the component body and connection parts.
[0043] 2. Design the needle-punched structure C / SiC-ZrC patch material as a trapezoidal hexahedron matching the groove of the component, and the component and the patch material are connected by threads to complete the physical connection.
[0044] 3. Use high-temperature adhesive to coat all connecting parts and surfaces. The adhesive contains Si, C, and O, which can meet the requirements of 1200°C.
[0045] 4. Install patch.
[0046] 5. Use the PIP process for online connection, the solution used is the SiBCN precursor solution, repeat the PIP process twice to complete the reinforcement.
[0047] The continuous carbon fiber toughened ceramic matrix composite member (referred to as sample ...
Embodiment 2
[0051] This embodiment provides a continuous carbon fiber reinforced ceramic matrix composite reinforcement method, the specific process is as follows:
[0052] 1. Use acetone to clean the body of the damaged component needle-punched C / SiC-ZrC component, including the connection part.
[0053] 2. Flare the damaged part into a circular shape, and the patch material is punctured C / SiC-ZrC-HfC-TaC composite material, which is designed to be cylindrical, and the patch material and the component body are connected by threads.
[0054] 3. Use high-temperature adhesive to coat all connecting parts and surfaces. The adhesive contains Si, C, and O, which can meet the requirements of 1200°C.
[0055] 4. Install patch.
[0056] 5. Use PIP process for online connection, use PCS solution for connection, repeat PIP process 3 times.
[0057] 6. Manually polish the surface to remove excess such as steps.
[0058] 7. The SiC coating is prepared by the overall CVD process to complete the rei...
Embodiment 3
[0063] This embodiment provides a continuous carbon fiber reinforced ceramic matrix composite reinforcement method, the specific process is as follows:
[0064] 1. For the new acupuncture structure C / SiC-ZrB 2 The component body is cleaned with ethanol, including the joints.
[0065] 2. The acupuncture structure C / SiC-HfB 2 -TaB 2 The patch material is designed as a trapezoidal hexahedron matching the groove of the component, and the component body and the patch material are connected by screws to complete the physical connection.
[0066] 3. Use high-temperature adhesive to coat all connecting parts and surfaces. The adhesive contains Si, C, O, and B, which can meet the requirements of 1200°C.
[0067] 4. Install patch.
[0068] 5. Use the PIP process for online connection. The solution used is the SiBCN precursor solution. Repeat the PIP process 4 times to complete the reinforcement.
[0069] Acupuncture the present embodiment C / SiC-HfB 2 -TaB 2 The continuous carbon ...
PUM
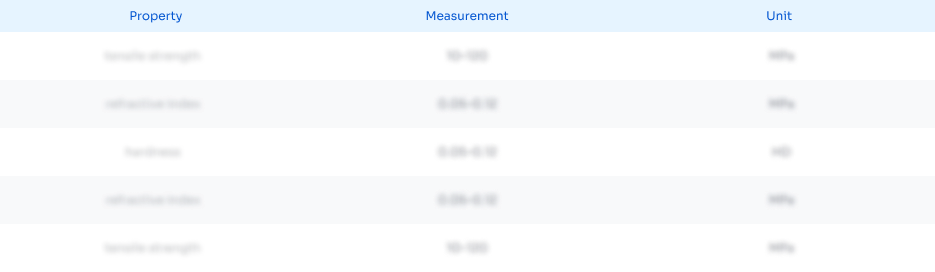
Abstract
Description
Claims
Application Information

- Generate Ideas
- Intellectual Property
- Life Sciences
- Materials
- Tech Scout
- Unparalleled Data Quality
- Higher Quality Content
- 60% Fewer Hallucinations
Browse by: Latest US Patents, China's latest patents, Technical Efficacy Thesaurus, Application Domain, Technology Topic, Popular Technical Reports.
© 2025 PatSnap. All rights reserved.Legal|Privacy policy|Modern Slavery Act Transparency Statement|Sitemap|About US| Contact US: help@patsnap.com