Modification method of graphite negative plate of lithium ion battery
A technology for lithium-ion batteries and graphite negative electrodes, applied in battery electrodes, negative electrodes, secondary batteries, etc., can solve the problems of cumbersome process, increase of specific surface area and defects, and decrease of Coulombic efficiency, etc., and achieve simple and controllable preparation process, The effect of excellent cycle performance and excellent rate performance
- Summary
- Abstract
- Description
- Claims
- Application Information
AI Technical Summary
Problems solved by technology
Method used
Image
Examples
Embodiment 1
[0021] Flake graphite will be used as the graphite electrode material to prepare graphite electrode sheets. Using a 1064nm laser, with an output power of 10w and a scanning speed of 10cm / s, set a preset area for laser focus spot scanning on the flake graphite electrode sheet, and perform laser etching under a certain atmosphere to obtain the final graphite electrode sheet.
[0022] The graphite electrode sheet exhibits a discharge specific capacity of 364mAh / g at a current density of 50mA / g, and still has a capacity of 210mA / g at a current density of 1A / g.
Embodiment 2
[0024] Graphitized onion carbon will be used as graphite electrode material to prepare graphite electrode sheet. Using a 1064nm laser, with an output power of 10w and a scanning speed of 10cm / s, set a preset area for laser focus spot scanning on the flake graphite electrode sheet, and perform laser etching under a certain atmosphere to obtain the final graphite electrode sheet.
[0025] as attached figure 1 The graphitized onion carbon anode before and after laser modification shown shows good rate performance.
[0026] The graphite electrode sheet exhibits a discharge specific capacity of 402mAh / g at a current density of 50mA / g, and still has a capacity of 265mA / g at a current density of 1A / g.
Embodiment 3
[0028] Graphitized onion carbon will be used as graphite electrode material to prepare graphite electrode sheet. Using a 450nm laser, with an output power of 5w and a scanning speed of 10cm / s, set a preset area for laser focus spot scanning on the flake graphite electrode sheet, and perform laser etching under a certain atmosphere to obtain the final graphite electrode sheet.
[0029] The graphite electrode sheet exhibits a discharge specific capacity of 371 mAh / g at a current density of 50 mA / g, and still has a capacity of 205 mA / g at a current density of 1 A / g.
PUM
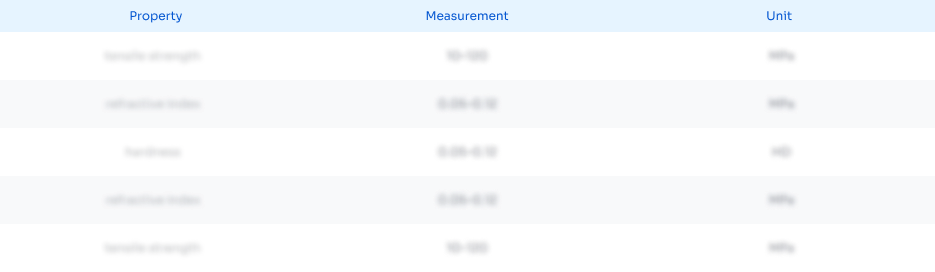
Abstract
Description
Claims
Application Information

- R&D
- Intellectual Property
- Life Sciences
- Materials
- Tech Scout
- Unparalleled Data Quality
- Higher Quality Content
- 60% Fewer Hallucinations
Browse by: Latest US Patents, China's latest patents, Technical Efficacy Thesaurus, Application Domain, Technology Topic, Popular Technical Reports.
© 2025 PatSnap. All rights reserved.Legal|Privacy policy|Modern Slavery Act Transparency Statement|Sitemap|About US| Contact US: help@patsnap.com