Fabric texture matt glaze, matt frit, ceramic tile, application and preparation method
A matte glaze and texture technology, applied in the field of ceramic tiles, can solve the problems of monotonous glaze and achieve the effect of solving light pollution
- Summary
- Abstract
- Description
- Claims
- Application Information
AI Technical Summary
Problems solved by technology
Method used
Image
Examples
preparation example Construction
[0038] The preparation method of the matte frit of cloth art texture matte glaze comprises the following steps:
[0039] The raw materials of the matt frit are centrifugally stirred evenly, and then transferred to a furnace at 1535°C-1555°C for heat preservation, so that the matte frit melt is homogenized, and then quenched in water and dried to obtain a matt frit.
[0040] A fabric texture matte glaze, comprising: 60-80% base glaze and 20-40% matte frit;
[0041] The matte frit is the matte frit of the above-mentioned fabric texture matte glaze.
[0042] The basic glaze of this solution can be replaced by a known glaze, and when combined with a matte frit, the glaze can be made into a ceramic tile with a matte texture, a texture of fabric, anti-fouling, anti-slip, acid and alkali corrosion resistance, wear resistance and high hardness.
[0043] More preferably, according to mass percentage, its raw materials include: 0-20% ultrawhite albite, 15-20% ultrawhite potassium felds...
Embodiment A
[0064] Preparation method of fabric texture matte tile
[0065] To prepare the top glaze:
[0066] The surface glaze is selected from the existing formula, and the raw materials include: 7 parts of air-knife soil, 34 parts of potassium feldspar, 11 parts of albite, 15 parts of burnt soil, 10 parts of quartz powder, 12 parts of calcined alumina, in parts by weight, 3 parts of dolomite, 8 parts of frit A, 8 parts of zirconium silicate, add water to account for 40% of the mass, after ball milling, sieving, iron removal, control the flow rate of ball glaze slurry for 50-80 seconds, specific gravity 1.88, 325 mesh sieve The remaining 0.5-1.0g / specific gravity cup. The top glaze is applied on the surface of the green body through the glaze pouring process to form a top glaze layer.
[0067] Preparation of fabric texture matte glaze:
[0068] (1) The raw materials of the matt frit are centrifugally stirred evenly, and then transferred to a melting furnace at 1535° C. for 100 minut...
Embodiment B
[0081] 1. Prepare the top glaze:
[0082] The present embodiment B1-B2 and comparative example B1 select the surface glaze, according to parts by weight, including: 7 parts of air knife soil, 34 parts of potassium feldspar, 11 parts of albite, 15 parts of burnt soil, 10 parts of quartz powder, calcined 12 parts of alumina, 3 parts of dolomite, 8 parts of frit A, and 8 parts of zirconium silicate. Add water to account for 40% of the mass. After ball milling, sieving, and iron removal, the flow rate of the ball glaze slurry is controlled for 50-80 seconds, the specific gravity is 1.88, and the remaining 0.5-1.0g / specific gravity cup is 325 mesh sieve. The top glaze is applied on the surface of the green body through the glaze pouring process to form a top glaze layer.
[0083] 2. Prepare the inkjet layer, apply the textured inkjet layer on the surface of the glaze layer by inkjet printing.
[0084] 3. Prepare the color-boosting glaze layer, which is applied to the surface of t...
PUM
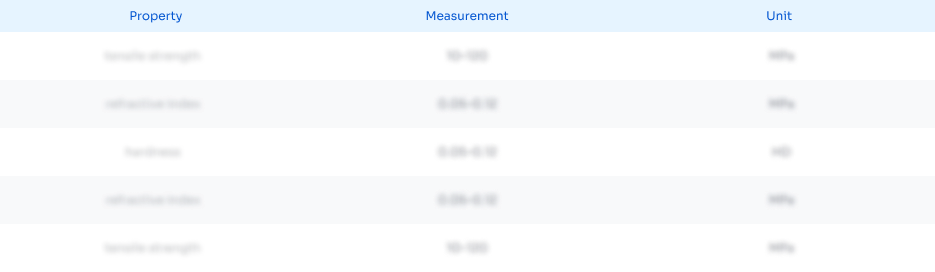
Abstract
Description
Claims
Application Information

- Generate Ideas
- Intellectual Property
- Life Sciences
- Materials
- Tech Scout
- Unparalleled Data Quality
- Higher Quality Content
- 60% Fewer Hallucinations
Browse by: Latest US Patents, China's latest patents, Technical Efficacy Thesaurus, Application Domain, Technology Topic, Popular Technical Reports.
© 2025 PatSnap. All rights reserved.Legal|Privacy policy|Modern Slavery Act Transparency Statement|Sitemap|About US| Contact US: help@patsnap.com