Thin film preparation system
A technology for thin film preparation and thin film deposition device, applied in the field of thin film preparation system based on vacuum environment, can solve problems such as unusable materials and elements, no reliable and stable evaporation source, and overall device damage.
- Summary
- Abstract
- Description
- Claims
- Application Information
AI Technical Summary
Problems solved by technology
Method used
Image
Examples
example 1
[0097] Coal is used as a raw material to generate liquid benzene, a precursor material to be evaporated, and graphene is produced by using the liquid benzene, wherein the liquid benzene is a low vapor pressure liquid material. Specifically, such as figure 1 As shown, the precursor preparation device, that is, the distillation device, is used to generate liquid benzene, the precursor material to be evaporated, from coal. The liquid benzene flows into the storage device through the second pipeline, and the liquid benzene is evaporated by the temperature control device of the evaporation control device to form gaseous benzene. Molecules, using a control mechanism to control the rate at which gaseous benzene molecules pass into the film deposition device through the first pipeline, wherein the film deposition device is chemical vapor deposition equipment. Gaseous benzene molecules were prepared as graphene films using chemical vapor deposition equipment. Among them, the growth pa...
example 2
[0100] Using the thin film preparation system of the embodiment of the present invention, a molecular beam epitaxy thin film deposition device is used to prepare an ordered nitrogen-doped graphene material using a low vapor pressure pentachloropyridine material.
[0101] Since the evaporation temperature of the pentachloropyridine material is lower than room temperature in a vacuum environment, the traditional molecular beam epitaxy method cannot be directly controlled by the evaporation of the k-cell evaporation source, and the condensed pentachloropyridine molecules destroy the vacuum chamber. Using the thin film preparation system of the present invention, the pentachloropyridine material is heat-treated through the temperature control device of the storage device, and the evaporation rate of the pentachloropyrimidine molecule is controlled by the evaporation control device, and the pentachloropyridine molecule is directly adsorbed on Cu(111) at room temperature On the surfa...
example 3
[0103] Utilize the thin film preparation system of the embodiment of the present invention, wherein the thin film deposition device adopts the molecular beam epitaxy thin film deposition device, utilizes chlorine molecule to be at room temperature and under the ultra-high vacuum environment (background vacuum is better than 1×10 -7 Pa) into the Cu (111) substrate (vacuum of 1 × 10 -5 Pa, 5 minutes), prepare Cl / Cu(111) alloy material at room temperature. In an ultra-high vacuum environment at room temperature, chlorine molecules are close to a liquid state. The traditional gas release method is difficult to control, and the storage device and the evaporation control device of the thin film preparation system of the present invention can be used to accurately control the dosage of chlorine molecules released in an ultra-high vacuum environment (can be accurately controlled at 5×10 -7 to 1×10 -1 Pa range), the scanning electron microscope image of the prepared Cl / Cu(111) alloy ...
PUM
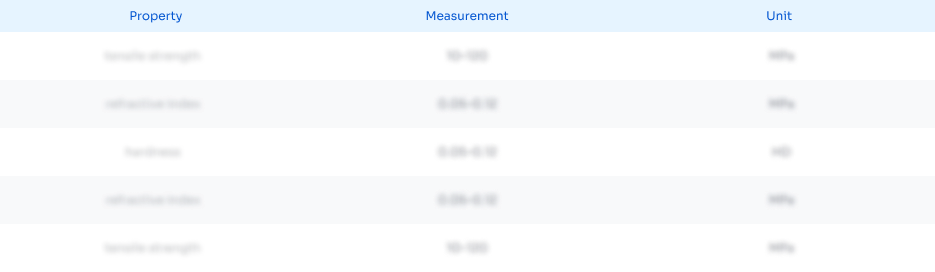
Abstract
Description
Claims
Application Information

- Generate Ideas
- Intellectual Property
- Life Sciences
- Materials
- Tech Scout
- Unparalleled Data Quality
- Higher Quality Content
- 60% Fewer Hallucinations
Browse by: Latest US Patents, China's latest patents, Technical Efficacy Thesaurus, Application Domain, Technology Topic, Popular Technical Reports.
© 2025 PatSnap. All rights reserved.Legal|Privacy policy|Modern Slavery Act Transparency Statement|Sitemap|About US| Contact US: help@patsnap.com