Composite board integrated wall module and installation method thereof
An installation method and integrated wall technology, applied in the field of architectural decoration, can solve problems such as poor sound insulation effect, complicated processing and installation, and damage to ALC boards, and achieve good sound insulation effect, high installation flatness, and improved installation efficiency.
- Summary
- Abstract
- Description
- Claims
- Application Information
AI Technical Summary
Problems solved by technology
Method used
Image
Examples
Embodiment 1
[0061] figure 1 and figure 2 All are three-dimensional structural schematic diagrams of a composite board integrated wall module disclosed in the present invention, image 3 and Figure 4 All are structural representations of decorative panels in the present invention, Figure 5 It is a schematic diagram of the enlarged structure of the top keel A in the present invention, Figure 6 It is a schematic diagram of the enlarged structure of vertical slats in the present invention, Figure 7 for Figure 6 Schematic diagram of the partially enlarged structure at A, Figure 8 It is a schematic diagram of the cross-sectional structure of the connecting gap between the vertical strip board C and the vertical strip board D in the present invention, as Figure 1 to Figure 8 Shown is a composite board integrated wall module and its installation method. The modular wall includes: a sky keel, a ground keel, a wall A1 and a wall B11, and the sky keel and the ground keel are respective...
Embodiment 2
[0063] figure 1 and figure 2 All are three-dimensional structural schematic diagrams of a composite board integrated wall module disclosed in the present invention, image 3 and Figure 4 All are structural representations of decorative panels in the present invention, Figure 5 It is a schematic diagram of the enlarged structure of the top keel A in the present invention, Figure 6 It is a schematic diagram of the enlarged structure of vertical slats in the present invention, Figure 7 for Figure 6 Schematic diagram of the partially enlarged structure at A, Figure 8 It is a schematic diagram of the cross-sectional structure of the connecting gap between the vertical strip board C and the vertical strip board D in the present invention, as Figure 1 to Figure 8 Shown is a composite board integrated wall module and its installation method. The vertical strip board B3 in the modular wall is provided with a wire groove 26, and an electric unit is installed inside the wir...
Embodiment 3
[0065] figure 1 and figure 2 All are three-dimensional structural schematic diagrams of a composite board integrated wall module disclosed in the present invention, image 3 and Figure 4 All are structural representations of decorative panels in the present invention, Figure 5 It is a schematic diagram of the enlarged structure of the top keel A in the present invention, Figure 6 It is a schematic diagram of the enlarged structure of vertical slats in the present invention, Figure 7 for Figure 6 Schematic diagram of the partially enlarged structure at A, Figure 8 It is a schematic diagram of the cross-sectional structure of the connecting gap between the vertical strip board C and the vertical strip board D in the present invention, as Figure 1 to Figure 8 In the shown composite board integrated wall module and its installation method, a card slot 18 is formed in the sky keel and the ground keel along the length direction of the wall A1, and the wall A1 is insert...
PUM
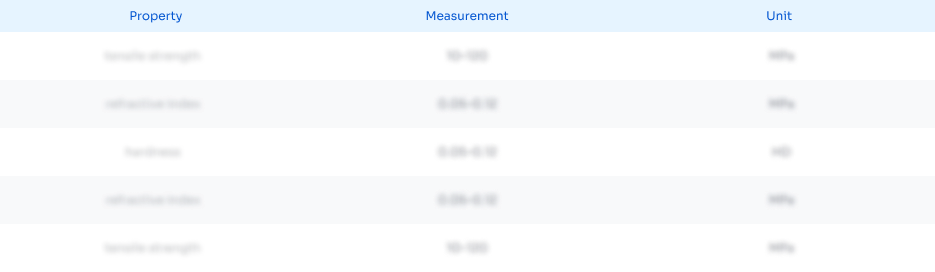
Abstract
Description
Claims
Application Information

- R&D
- Intellectual Property
- Life Sciences
- Materials
- Tech Scout
- Unparalleled Data Quality
- Higher Quality Content
- 60% Fewer Hallucinations
Browse by: Latest US Patents, China's latest patents, Technical Efficacy Thesaurus, Application Domain, Technology Topic, Popular Technical Reports.
© 2025 PatSnap. All rights reserved.Legal|Privacy policy|Modern Slavery Act Transparency Statement|Sitemap|About US| Contact US: help@patsnap.com