Modified cellulose spunlace non-woven fabric and preparation method thereof
A technology of spunlace non-woven fabric and cellulose, applied in the direction of plant fiber, fiber treatment, fiber type, etc., can solve the problems of poor durability and poor mechanical properties of spunlace non-woven fabric, so as to improve the mechanical properties and improve the The effect of photocatalytic antibacterial performance and improving the performance of decomposing formaldehyde
- Summary
- Abstract
- Description
- Claims
- Application Information
AI Technical Summary
Problems solved by technology
Method used
Image
Examples
preparation example 1
[0035] Preparation Example 1 Modified Cellulose
[0036] Synthetic route such as figure 1 , the preparation method is as follows:
[0037] S1. Cellulose treatment: Soak 50g of cellulose in 200mL of petroleum ether and ethyl acetate mixed solvent (the volume ratio of petroleum ether and ethyl acetate is 3:2) for 1h, filter, dry, and then add 100mL of silane In the aqueous ethanol solution of coupling agent KH550 (the content of KH550 is 3wt%, the content of ethanol is 35wt%, and the balance is water), add ammonia water dropwise to adjust the pH value to 8, react for 0.5h, filter, and dry at 120°C for 0.5 h, then placed in 100mL ethanol, ultrasonically cleaned for 0.5h, filtered, and dried to obtain surface-grafted cellulose;
[0038] S2. Preparation of intermediate: Dissolve 20g of 3-bromopropylamine in 200mL of dichloromethane, add 100g of surface-grafted cellulose prepared in step S1, heat to 30°C under nitrogen protection, stir for 2h, filter, and use Wash with ethanol an...
preparation example 2
[0040] Preparation Example 2 Modified Cellulose
[0041] Synthetic route such as figure 1 , the preparation method is as follows:
[0042] S1. Cellulose treatment: Soak 50g of cellulose in 200mL of petroleum ether and ethyl acetate mixed solvent (the volume ratio of petroleum ether and ethyl acetate is 5:2) for 2h, filter, dry, and then add 100mL of silane In the ethanol aqueous solution of coupling agent KH550 (the content of KH550 is 5wt%, the content of ethanol is 40wt%, and the balance is water), ammonia water is added dropwise to adjust the pH value to 9, react for 1h, filter, and dry at 140°C for 1h, Then placed in 100mL ethanol, ultrasonically cleaned for 1h, filtered, and dried to obtain surface-grafted cellulose;
[0043] S2. Preparation of intermediate: Dissolve 40g of 3-bromopropylamine in 200mL of dichloromethane, add 100g of surface-grafted cellulose prepared in step S1, heat to 50°C under nitrogen protection, stir for 4h, filter, and use Wash with ethanol and dr...
preparation example 3
[0045] Preparation Example 3 Modified Cellulose
[0046] Synthetic route such as figure 1 , the preparation method is as follows:
[0047] S1. Treatment of cellulose: Soak 50g of cellulose in 200mL of petroleum ether and ethyl acetate mixed solvent (the volume ratio of petroleum ether and ethyl acetate is 4:2) for 1.5h, filter, dry, and then add 100mL of Silane coupling agent KH550 in ethanol aqueous solution (the content of KH550 is 4wt%, the content of ethanol is 37wt%, and the balance is water), add ammonia water dropwise to adjust the pH value to 8.5, react for 1h, filter, and dry at 130°C for 1h , then placed in 100mL ethanol, ultrasonically cleaned for 1h, filtered, and dried to obtain surface-grafted cellulose;
[0048] S2. Preparation of intermediate: Dissolve 30g of 3-bromopropylamine in 200mL of dichloromethane, add 100g of surface-grafted cellulose prepared in step S1, heat to 40°C under nitrogen protection, stir for 3h, filter, and use Wash with ethanol and dry ...
PUM
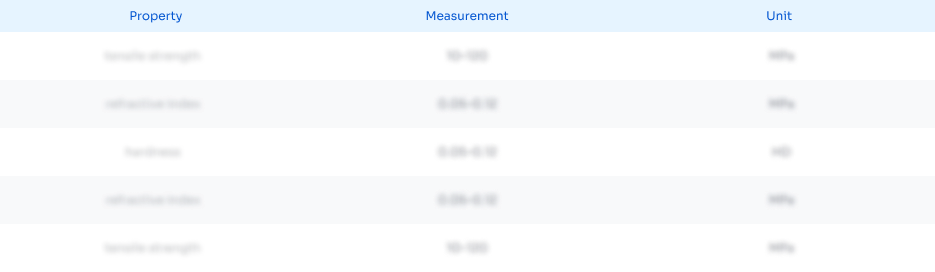
Abstract
Description
Claims
Application Information

- R&D
- Intellectual Property
- Life Sciences
- Materials
- Tech Scout
- Unparalleled Data Quality
- Higher Quality Content
- 60% Fewer Hallucinations
Browse by: Latest US Patents, China's latest patents, Technical Efficacy Thesaurus, Application Domain, Technology Topic, Popular Technical Reports.
© 2025 PatSnap. All rights reserved.Legal|Privacy policy|Modern Slavery Act Transparency Statement|Sitemap|About US| Contact US: help@patsnap.com