System and method for co-production of dimethyl carbonate and dihydric alcohol
A dimethyl carbonate, diol technology, applied in the purification/separation of carbonate/haloformate, organic carbonate preparation, chemical instruments and methods, etc., can solve the problem of high production cost and energy efficiency of DMC Low and no energy coupling utilization, etc., to achieve the effect of reducing methanol distillation and circulation, improving energy coupling degree, and improving energy connection efficiency
- Summary
- Abstract
- Description
- Claims
- Application Information
AI Technical Summary
Problems solved by technology
Method used
Image
Examples
Embodiment 1
[0079] refer to figure 1 , the present embodiment provides a system for the co-production of dimethyl carbonate and dibasic alcohols, including a transesterification unit, methanol and dimethyl carbonate azeotrope separation unit, and methanol, dibasic alcohols and catalyst separation unit 400 , the transesterification reaction unit is composed of a reactive distillation column 100, and the methanol and dimethyl carbonate azeotrope separation unit is composed of a first azeotropic distillation column 200 and a second azeotropic distillation column 300, so The methanol, dibasic alcohol and catalyst separation unit 400 are used to realize methanol recovery, dibasic alcohol refining, catalyst recovery and by-product recovery, and the top of the reactive distillation column 100 uses methanol and dimethyl carbonate azeotrope material 4 into the first azeotropic rectification tower 200, the reactive distillation tower bottom extraction material 5 of the reactive rectification tower...
Embodiment 2
[0095] The present embodiment provides a kind of method of coproduction dimethyl carbonate and dibasic alcohol, adopts such as figure 1 Shown system carries out, and the method for described coproduction dimethyl carbonate and dibasic alcohol comprises the following steps:
[0096] A. Transesterification reaction:
[0097] The vinyl carbonate material 1, the methanol material 3 and the catalyst material 2 enter the reactive distillation tower 100, and the methanol material 3 and the carbonic ester material 1 undergo a transesterification reaction under the action of the catalyst material 2, and the reactive distillation tower 100 Extract methanol and dimethyl carbonate azeotrope material 4 from the top of the tower, extract material 5 from the bottom of the reactive distillation tower 100, extract material 5 from the bottom of the reactive distillation tower 100, and extract material 5 from the bottom of the reactive distillation tower Liquid mixtures comprising methanol, et...
PUM
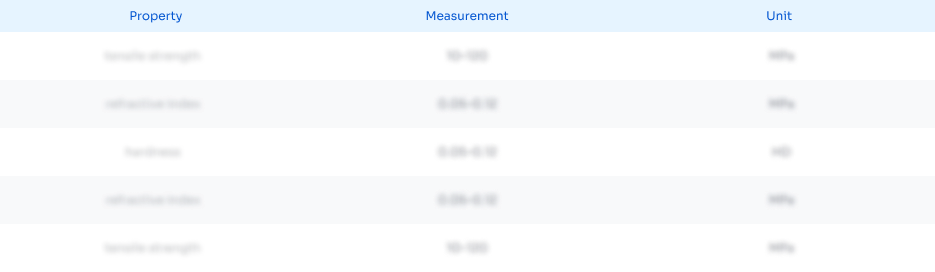
Abstract
Description
Claims
Application Information

- R&D
- Intellectual Property
- Life Sciences
- Materials
- Tech Scout
- Unparalleled Data Quality
- Higher Quality Content
- 60% Fewer Hallucinations
Browse by: Latest US Patents, China's latest patents, Technical Efficacy Thesaurus, Application Domain, Technology Topic, Popular Technical Reports.
© 2025 PatSnap. All rights reserved.Legal|Privacy policy|Modern Slavery Act Transparency Statement|Sitemap|About US| Contact US: help@patsnap.com