Crosslinked polyethylene cable insulating material containing compounding agent with high electrical resistance and preparation method thereof
A cross-linked polyethylene, cable insulation technology, applied in insulators, organic insulators, plastic/resin/wax insulators, etc., can solve the problem of long-term compatibility of high-efficiency polymers in a wide temperature range of voltage stabilizers, etc. The effect of dense electron-withdrawing space action range, improved resistance to electric tree branches, and increased action space range
- Summary
- Abstract
- Description
- Claims
- Application Information
AI Technical Summary
Problems solved by technology
Method used
Image
Examples
Embodiment 1
[0032] Put 40g of low-density polyethylene into the internal mixer, melt at 110°C, and rotate at a speed of 50r / min, add 0.32g of 4-propenyloxy-2-hydroxybenzophenone after it melts, at the same temperature and Mix for 5 minutes at a rotating speed, then add 0.8g of dicumyl peroxide and 0.12g of antioxidant 1035, continue mixing for 3 minutes at the same temperature and rotating speed, and carry out melt blending. After obtaining the blend, put it into The mold is hot-pressed in a flat vulcanizer at 110°C and 15MPa, and then crosslinked in a flat vulcanizer at 175°C and 15MPa for 30 minutes to complete the crosslinking reaction of crosslinked polyethylene and the grafting of aromatic ketone compounds containing chelating rings. reaction to obtain a chelating ring aromatic ketone grafted cross-linked polyethylene insulating material. Specific process such as figure 1 As shown, the initiator dicumyl peroxide decomposes at high temperature to produce primary free radicals, and th...
Embodiment 2
[0038] Put 10kg of low-density polyethylene into the double-cone rotary vacuum dryer, set the internal temperature of the dryer to 90°C, and the rotation speed to 50r / min, preheat the low-density polyethylene particles for 10min, add 30g of antioxidant 1076, 40g of 4-propylene Oxy-2-hydroxybenzophenone and 180g of dicumyl peroxide are stirred evenly and heated to 90°C until the three powders are completely melted into a solution. After the solution is stirred evenly, spray it into a double-cone rotary vacuum dryer. Rotate, heat and soak for 4 hours under 0.1MPa vacuum, put the soaked granules into the parallel twin-screw extruder, extrude and granulate at 110 degrees Celsius, put the obtained granules into the mold and heat them in a flat vulcanizer at 110°C and 15MPa Compression molding, and then cross-linking in a flat vulcanizing machine at 175°C and 15MPa for 30 minutes to complete the cross-linking reaction of cross-linked polyethylene and the grafting reaction of aromatic...
Embodiment 3
[0040] Put 100kg of low-density polyethylene into the double-cone rotary vacuum dryer, set the internal temperature of the dryer to 80°C, and the rotation speed to 50r / min, preheat the low-density polyethylene particles for 10min, add 300g of antioxidant 1035, 200g of 2-acrylic acid 2-(4-benzoyl-3-hydroxyphenoxy)ethyl ester, 200g 2-propenyl-4,6-bibenzoylresorcinol, 1800g dicumyl peroxide were stirred evenly and heated to 90°C until the three powders are completely melted into a solution. Stir the solution evenly, spray it into a double-cone rotary vacuum dryer, rotate and heat it for 8 hours under a vacuum of -0.1MPa, and put the soaked particles into a single-screw extruder. Extrude and granulate at 110°C, and use the obtained granules as insulating material granules to extrude and cover the cable conductor cores with a three-layer co-extrusion extruder to make insulating cores with inner and outer shielding layers, and then the insulating cores Pull into the high-temperature...
PUM
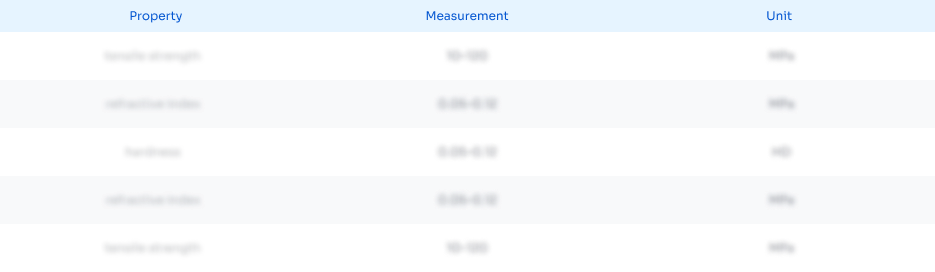
Abstract
Description
Claims
Application Information

- R&D
- Intellectual Property
- Life Sciences
- Materials
- Tech Scout
- Unparalleled Data Quality
- Higher Quality Content
- 60% Fewer Hallucinations
Browse by: Latest US Patents, China's latest patents, Technical Efficacy Thesaurus, Application Domain, Technology Topic, Popular Technical Reports.
© 2025 PatSnap. All rights reserved.Legal|Privacy policy|Modern Slavery Act Transparency Statement|Sitemap|About US| Contact US: help@patsnap.com