Modified graphene oxide material as well as preparation method and application thereof
A technology of graphene and stone oxide, applied in epoxy resin coatings, anti-corrosion coatings, coatings, etc., can solve problems such as hindering the application of graphene oxide and poor dispersion performance
- Summary
- Abstract
- Description
- Claims
- Application Information
AI Technical Summary
Problems solved by technology
Method used
Image
Examples
Embodiment 1
[0045] (1) Preparation of amino-functionalized graphene oxide
[0046] 5g of γ-aminopropyltriethoxysilane, 5g of N-aminoethyl-γ-aminopropyltrimethoxysilane and 10g of graphene oxide were reacted at 50°C for 5 hours to obtain amino-functionalized graphene oxide.
[0047] (2) Preparation of nonionic epoxy emulsifier
[0048] Mix 80g toluene, 10g methyl acrylate, 5g ethyl acrylate, 10g butyl methacrylate, 5g isobutyl methacrylate, 30g allyl polyether and 20g glycidyl methacrylate, add 0.2g initiator Agent azobisisobutyronitrile, react at 110°C for 3 hours to obtain a nonionic epoxy emulsifier.
[0049] (3) Preparation of modified graphene oxide material and epoxy resin emulsion
[0050] The amino-functionalized graphene oxide 10g prepared by step (1) and the nonionic epoxy emulsifier 100g prepared by step (2) were reacted under ultrasonication for 0.8h, and the solvent was removed by rotary evaporation at 110°C for 0.8h. A modified graphene oxide material is obtained.
[0051...
Embodiment 2
[0054] (1) Preparation of amino-functionalized graphene oxide
[0055] 15g of γ-aminopropyltrimethoxysilane, 5g of N-aminoethyl-γ-aminopropylmethyldimethoxysilane and 10g of graphene oxide were reacted at 30°C for 3 hours to obtain amino-functionalized graphene oxide .
[0056] (2) Preparation of nonionic epoxy emulsifier
[0057] Mix 40g toluene, 10g benzene, 5g methyl acrylate, 5g butyl acrylate, 5g methyl methacrylate, 5g ethyl methacrylate, 30g allyl polyether and 10g glycidyl methacrylate, add 0.2 g of azobisisoheptanonitrile and 0.3g of azobisisobutyronitrile were reacted at 120°C for 5 hours to obtain a nonionic epoxy emulsifier.
[0058] (3) Preparation of modified graphene oxide material and epoxy resin emulsion
[0059] The amino-functionalized graphene oxide 20g prepared by step (1) and the nonionic epoxy emulsifier 100g prepared by step (2) were reacted under ultrasonication for 1h, and the solvent was removed by rotary evaporation at 120°C for 0.5h to obtain M...
Embodiment 3
[0063] (1) Preparation of amino-functionalized graphene oxide
[0064] React 15g N-aminoethyl-γ-aminopropyltriethoxysilane, 10g N-aminoethyl-γ-aminopropylmethyldiethoxysilane and 10g graphene oxide at 60°C for 2 hours , to obtain amino-functionalized graphene oxide.
[0065] (2) Preparation of nonionic epoxy emulsifier
[0066] Mix 100g of solvent butanone, 5g of methyl acrylate, 5g of isobutyl acrylate, 3g of ethyl methacrylate, 2g of butyl methacrylate, 50g of allyl polyether and 5g of glycidyl methacrylate, and add 0.5 g azobisisobutyronitrile, 0.3g azobisisoheptanonitrile, and react at 80°C for 8 hours to obtain a nonionic epoxy emulsifier.
[0067] (3) Preparation of modified graphene oxide material and epoxy resin emulsion
[0068] The amino-functionalized graphene oxide 15g prepared by step (1) and the nonionic epoxy emulsifier 100g prepared by step (2) were reacted for 2h under the action of ultrasound, and the solvent was removed by rotary evaporation at 80°C for 1...
PUM
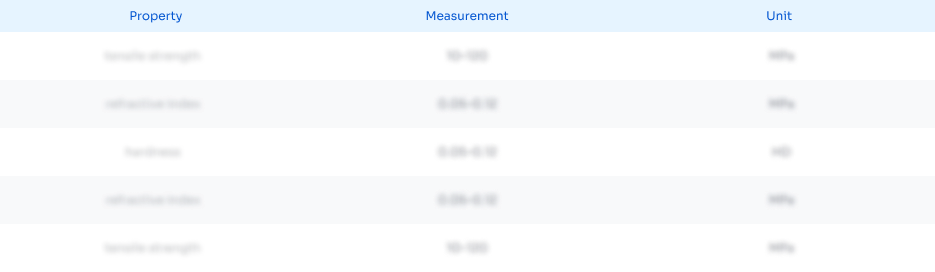
Abstract
Description
Claims
Application Information

- R&D Engineer
- R&D Manager
- IP Professional
- Industry Leading Data Capabilities
- Powerful AI technology
- Patent DNA Extraction
Browse by: Latest US Patents, China's latest patents, Technical Efficacy Thesaurus, Application Domain, Technology Topic, Popular Technical Reports.
© 2024 PatSnap. All rights reserved.Legal|Privacy policy|Modern Slavery Act Transparency Statement|Sitemap|About US| Contact US: help@patsnap.com