Sulfur-containing benzophenone polyurethane modified epoxy acrylate self-initiation UV resin
A technology of sulfur benzophenone polyurethane and epoxy acrylate, which is applied in the field of modified self-initiating photocuring resin, sulfur-containing benzophenone polyurethane modified epoxy acrylate self-initiating UV resin and its preparation, can solve the problem of Produces irritating odor of toxic substances, easy yellowing of cured coating, easy migration to the surface and other problems, and achieves the effects of high self-initiation efficiency, improved storage stability, and excellent adhesion
- Summary
- Abstract
- Description
- Claims
- Application Information
AI Technical Summary
Problems solved by technology
Method used
Image
Examples
Embodiment 1
[0047] A kind of sulfur-containing benzophenone polyurethane modified epoxy acrylate self-initiated UV resin A1, and its preparation steps are as follows:
[0048] a) Preparation of epoxy acrylate E44A: Add 230.0 parts of bisphenol A epoxy resin E-44 into a four-necked flask equipped with a reflux condenser, a thermometer, a dropping funnel and a stirrer, and wait until the temperature rises to 80°C Slowly add dropwise a mixture of 72.0 parts of acrylic acid, 7.5 parts of N,N-dimethylaniline and 0.9 parts of p-hydroxyanisole, after the addition is complete, slowly raise the temperature to 85-90°C, keep the temperature for 3 hours, and then take samples every 40 minutes Detect the acid value of the system, stop the reaction when the detected acid value is lower than 4.6mgKOH / g, and prepare epoxy acrylate E44A;
[0049] b), preparation of isocyanate-acrylic acid functional monomer TDI-HEMA: add 87.0 parts of TDI-80 and 0.06 part of DBTDL in a four-necked flask equipped with a re...
Embodiment 2
[0056] A kind of sulfur-containing benzophenone polyurethane modified epoxy acrylate self-initiated UV resin A2, and its preparation steps are as follows:
[0057] a) Preparation of epoxy acrylate E51A: Add 78.4 parts of bisphenol A epoxy resin E-51 into a four-necked flask equipped with a reflux condenser, thermometer, dropping funnel and stirrer, and wait until the temperature rises to 80°C Slowly add dropwise a mixture of 34.4 parts of methacrylic acid, 2.8 parts of catalyst (the mass ratio of N,N-dimethylaniline to tetrabutylammonium bromide is 1:1) and 0.34 parts of p-hydroxyanisole, dropwise After completion, slowly raise the temperature to 85-90°C, keep it warm for 3 hours, then take samples every 30 minutes to detect the acid value of the system, stop the reaction when the detected acid value is lower than 5mgKOH / g, and prepare epoxy acrylate E51A;
[0058]b) Preparation of isocyanate-acrylic acid functional monomer IPDI-HEA: Add 44.5 parts of IPDI and 0.03 parts of DB...
Embodiment 3
[0065] A kind of sulfur-containing benzophenone polyurethane modified epoxy acrylate self-initiated UV resin A3, and its preparation steps are as follows:
[0066] a) Preparation of epoxy acrylate E51A: Add 78.4 parts of bisphenol A epoxy resin E-51 into a four-necked flask equipped with a reflux condenser, thermometer, dropping funnel and stirrer, and wait until the temperature rises to 80°C Slowly add dropwise a mixture of 34.4 parts of methacrylic acid, 2.8 parts of catalyst (the mass ratio of N,N-dimethylaniline to tetrabutylammonium bromide is 1:1) and 0.34 parts of p-hydroxyanisole, dropwise After completion, slowly raise the temperature to 85-90°C, keep it warm for 3 hours, then take samples every 30 minutes to detect the acid value of the system, stop the reaction when the detected acid value is lower than 5mgKOH / g, and prepare epoxy acrylate E51A;
[0067] b) Preparation of isocyanate-acrylic acid functional monomer HDI-HEA: Add 33.6 parts of HDI and 0.02 parts of DBT...
PUM
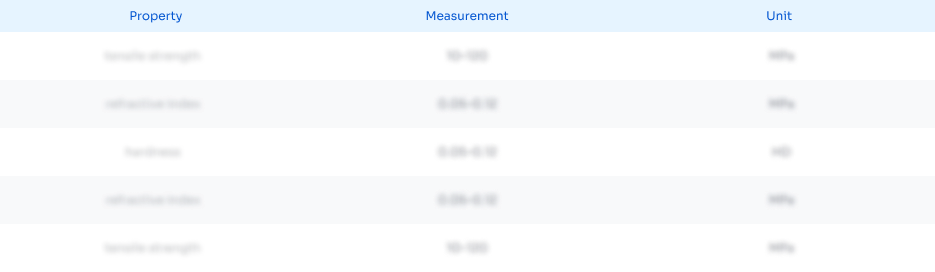
Abstract
Description
Claims
Application Information

- Generate Ideas
- Intellectual Property
- Life Sciences
- Materials
- Tech Scout
- Unparalleled Data Quality
- Higher Quality Content
- 60% Fewer Hallucinations
Browse by: Latest US Patents, China's latest patents, Technical Efficacy Thesaurus, Application Domain, Technology Topic, Popular Technical Reports.
© 2025 PatSnap. All rights reserved.Legal|Privacy policy|Modern Slavery Act Transparency Statement|Sitemap|About US| Contact US: help@patsnap.com