Method for preparing N,N,N',N'-tetra(beta-hydroxypropyl) adipamide
A technology of adipamide and hydroxypropyl, which is applied in the field of preparing N,N,N',N'-tetraadipamide, which can solve the problem of low separation efficiency of diisopropanolamine, high energy cost and product chromaticity uncontrollable issues
- Summary
- Abstract
- Description
- Claims
- Application Information
AI Technical Summary
Problems solved by technology
Method used
Examples
Embodiment 1
[0019] Add 166.3g of diisopropanolamine and 1.15g of potassium hydroxide into a glass reactor, stir and heat to a reaction temperature of 100°C, and drop 87.0g of dimethyl adipate into the reaction vessel under a vacuum condition of -0.099MPa. In the kettle, after the feed was completed, the stirring reaction was continued for 2 hours.
[0020] After the reaction was completed, the temperature of the material was lowered to 60 ° C, and under the condition of -0.099 MPa, 25.0 g of concentrated sulfuric acid was added dropwise. After stirring and crystallizing, diisopropanolamine sulfate was separated by filtration, and the filtrate was distilled to remove the ethanol solvent to obtain 169.7g of N,N,N',N'-tetrakis(β-hydroxypropyl)adipamide product, product yield It is 90.3%, and the product purity is 96.2%.
Embodiment 2
[0022] Add 199.5g of diisopropanolamine and 1.15g of potassium hydroxide into the glass reaction kettle, stir and heat to the reaction temperature of 100°C, and drop 87.0g of dimethyl adipate into the reaction under the vacuum condition of -0.099MPa In the kettle, after the feed was completed, the reaction was continued under reduced pressure and stirred for 2 hours.
[0023] After the reaction was completed, the temperature of the material was lowered to 80°C. Under the condition of vacuum -0.090, 50.0g of concentrated sulfuric acid was added dropwise. After the dropwise addition, the stirring was continued for 1 hour under this condition. After stirring and crystallizing, diisopropanolamine sulfate was separated by filtration, and the filtrate was distilled to remove the ethanol solvent to obtain 173.0g of N,N,N',N'-tetrakis(β-hydroxypropyl)adipamide product, the product yield It is 92.0%, and the product purity is 97.7%.
Embodiment 3
[0025] Add 266.0g of diisopropanolamine and 1.15g of potassium hydroxide into the glass reactor, stir and heat to the reaction temperature of 100°C, and drop 87.0g of dimethyl adipate into the reaction vessel under the vacuum condition of -0.099MPa In the kettle, after the feed was completed, the reaction was continued under reduced pressure and stirred for 2 hours.
[0026] After the reaction is completed, the temperature of the material is lowered to 80°C. Under the condition of -0.099MPa, 100g of concentrated sulfuric acid is added dropwise. After the dropwise addition, the stirring is continued for 1 hour under this condition, and then 700.0g of n-propanol is added, and the temperature is lowered to 25°C. After stirring and crystallizing, diisopropanolamine sulfate was separated by filtration, and the filtrate was removed by distillation to remove the n-propanol solvent to obtain 180.8g of N, N, N', N'-tetrakis (β-hydroxypropyl) adipamide product, The product yield is 96.2...
PUM
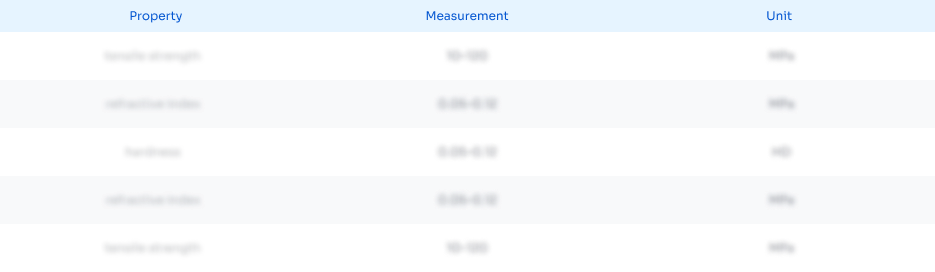
Abstract
Description
Claims
Application Information

- Generate Ideas
- Intellectual Property
- Life Sciences
- Materials
- Tech Scout
- Unparalleled Data Quality
- Higher Quality Content
- 60% Fewer Hallucinations
Browse by: Latest US Patents, China's latest patents, Technical Efficacy Thesaurus, Application Domain, Technology Topic, Popular Technical Reports.
© 2025 PatSnap. All rights reserved.Legal|Privacy policy|Modern Slavery Act Transparency Statement|Sitemap|About US| Contact US: help@patsnap.com