Production method for reducing grain boundary oxidation of hot continuous rolling 65Mn strip steel
A technology of grain boundary oxidation and production method, which is applied in the direction of metal rolling, metal rolling, workpiece heating device, etc., to meet the processing performance requirements, reduce the probability of grain boundary oxidation defects, and reduce the severity of the effect
- Summary
- Abstract
- Description
- Claims
- Application Information
AI Technical Summary
Problems solved by technology
Method used
Image
Examples
Embodiment
[0031] Smelting 65Mn steel, mold slag CaO / SiO 2 is 0.98. Composition of steel: C 0.66%, Si 0.20%, Mn 0.93%, P 0.015%, S 0.001%.
[0032] The size of the slab after continuous casting is 200*1250*12300mm.
[0033] The atmosphere in the third-stage furnace of the walking heating furnace is a weak oxidizing atmosphere, the air-fuel ratio is set to 1.9, and the furnace gas temperature is shown in Table 1.
[0034] Table 1:
[0035] Heating section 1. Heating section temperature, ℃ The temperature of the second heating section, ℃ Temperature of soaking section, ℃ upper part 1170 1310 1250 lower part 1160 1280 1230
[0036] See Table 2 for heating time in the furnace.
[0037] Table 2:
[0038]
[0039] The control of rolling parameters is shown in Table 3.
[0040] table 3:
[0041]
[0042] The metallographic examination of the three coils of steel samples shows that there is a partial decarburization layer, but there is no surface ...
PUM
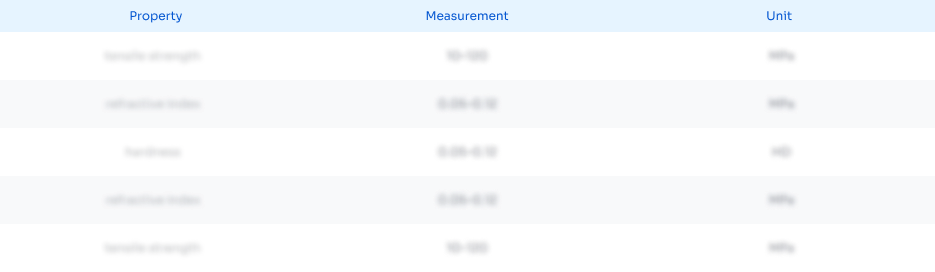
Abstract
Description
Claims
Application Information

- Generate Ideas
- Intellectual Property
- Life Sciences
- Materials
- Tech Scout
- Unparalleled Data Quality
- Higher Quality Content
- 60% Fewer Hallucinations
Browse by: Latest US Patents, China's latest patents, Technical Efficacy Thesaurus, Application Domain, Technology Topic, Popular Technical Reports.
© 2025 PatSnap. All rights reserved.Legal|Privacy policy|Modern Slavery Act Transparency Statement|Sitemap|About US| Contact US: help@patsnap.com