High-softness, high-toughness and cracking-resistant sheath material and preparation method thereof
A technology of sheath material and high toughness, applied in the field of high toughness and crack-resistant sheath material and its preparation, can solve the problems of sheath cracking and other problems, and achieve the effect of strong flexibility and high porosity
- Summary
- Abstract
- Description
- Claims
- Application Information
AI Technical Summary
Problems solved by technology
Method used
Image
Examples
Embodiment 1
[0045] A wire cable resistant to cracking with high toughness sheathing material and preparation method, comprising the steps of:
[0046] The first step: the spiral crimp fiber
[0047] The elastic fiber of polyolefin entire tank heated by the heating cylinder to 115 deg.] C, and then through the fiber coil crimper, spiral crimped fibers were prepared, to prepare a helix angle of the spiral crimped fibers is 66 degrees, a pitch of 1 m;
[0048] Step Two: helical crimped fiber crosslinked
[0049] The first step in processing a helical crimped fiber good irradiation crosslinking, electron accelerator energy level by 3.0 MeV electron accelerator, the irradiation dose of 15 million electron de;
[0050] The third step: the helical crimped fiber stretched styling
[0051] The second step after spiral crimped fibers crosslinked by pre-heating the tank to 160. deg.] C, and then uniform stretching, straightening the spiral crimped fibers, then cooled rapidly to room temperature by cooli...
Embodiment 2
[0056] In the same embodiment, the difference is:
[0057] In the fourth step: The composition of the polyolefin melt is: 30 kg linear low density polyethylene, 30 kg of three-membered ethylene rubber, 3kg silicone rubber, 15kg magnesium hydroxide, 0.8kg antioxidant 1010 #, 0.8kg antioxidant 168 #, 2kg Polyethylene Wax, 0.5 kg of methylphenyl silicone oil, 3kg white oil, 2kg masterbatch.
Embodiment 3
[0059] In the same embodiment, the difference is:
[0060] In the fourth step: The composition of the polyolefin melt is: 25 kg linear low-density polyethylene, 25 kg of three yuan ethylene ethylene rubber, 2.5kg silicone rubber, 13kg magnesium hydroxide, 0.65 kg antioxidant 1010 #, 0.65 kg antioxidant 168 #, 1.5kg Polyethylene wax, 0.4 kg of methylphenylsilicone oil, 2.5kg of white oil, 1.5kg of masterbatch.
[0061] Example 1-3 Preparation of Sheath Material Performance Test Comparison (taken from finished cable care cover) as shown in Table 1.
[0062] Table 1 Example 1-3 Preparation Sheet Material Performance
[0063]
PUM
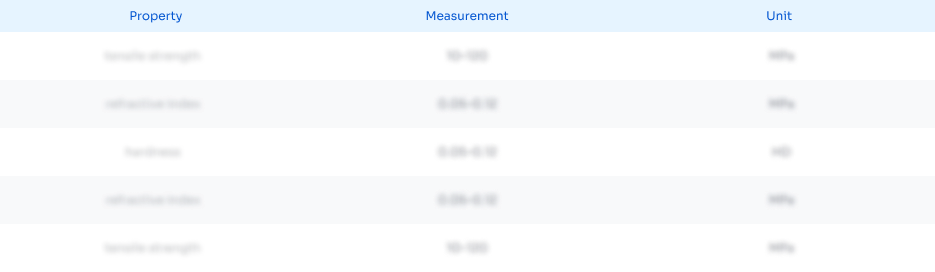
Abstract
Description
Claims
Application Information

- Generate Ideas
- Intellectual Property
- Life Sciences
- Materials
- Tech Scout
- Unparalleled Data Quality
- Higher Quality Content
- 60% Fewer Hallucinations
Browse by: Latest US Patents, China's latest patents, Technical Efficacy Thesaurus, Application Domain, Technology Topic, Popular Technical Reports.
© 2025 PatSnap. All rights reserved.Legal|Privacy policy|Modern Slavery Act Transparency Statement|Sitemap|About US| Contact US: help@patsnap.com