Modified polyaspartic acid ester DTM anticorrosive paint and preparation method thereof
A technology of aspartate and anti-corrosion coatings, applied in polyurea/polyurethane coatings, anti-corrosion coatings, coatings, etc., can solve the problems of poor adhesion to metal substrates, complicated construction process, shortened construction window, etc., and achieve waterproof And anti-corrosion performance is good, the preparation process is simple, the effect of wide construction window
- Summary
- Abstract
- Description
- Claims
- Application Information
AI Technical Summary
Problems solved by technology
Method used
Image
Examples
Embodiment 1
[0027] A kind of modified polyaspartic acid ester DTM anticorrosion coating, it comprises A component and B component, by weight, A component comprises 40 parts of polyaspartic acid esters, 30 parts of antirust base material, 4 parts Parts of additive A and 5 parts of solvent A (MOCA), wherein the fineness of the anti-rust base material is ≤25um, which includes 2 parts of pigment (rutile titanium dioxide), 6 parts of filler (1.2 parts of talc and 4.8 parts of barium sulfate) , 17 parts of polyaspartic acid ester, 2 parts of aluminum tripolyphosphate, 1 part of zinc phosphate, 2 parts of dispersant (BYK2155), additive A includes 1 part of defoamer (BYK1799) and 3 parts of UV absorber (1 Parts of Tinuvin 400 and 2 parts of Tinuvin 246); The B component is a hydrophilic modified polyisocyanate, which includes 80 parts of HDI trimer (48 parts of HDI uretdione isocyanate and 32 parts of HDI trimer isocyanate), 1 1 part of additive B (sulfonic acid monomer) and 1 part of solvent B (...
Embodiment 2
[0034] A kind of modified polyaspartic acid ester DTM anticorrosion paint, it comprises A component and B component, by weight, A component comprises 50 parts of polyaspartic acid esters, 35 parts of antirust base materials, 6 parts Parts of additive A and 10 parts of solvent A (MOCA), wherein the fineness of anti-rust base material is ≤25um, which includes 2.5 parts of pigment (rutile titanium dioxide), 7 parts of filler (1.4 parts of talcum powder and 5.6 parts of barium sulfate) , 19 parts of polyaspartic acid ester, 2.5 parts of aluminum tripolyphosphate, 1.5 parts of zinc phosphate, 2.5 parts of dispersant (BYK2155), additive A includes 1.5 parts of defoamer (BYK1799) and 4.5 parts of UV absorber (1.5 Parts of Tinuvin 400 and 3 parts of Tinuvin 246); The B component is a hydrophilic modified polyisocyanate, which includes 95 parts of HDI trimer (60.5 parts of HDI uretdione isocyanate and 34.5 parts of HDI trimer isocyanate), 2 Parts of additive B (sulfonic acid monomer) a...
Embodiment 3
[0037] A kind of modified polyaspartic acid ester DTM anticorrosion paint, it comprises A component and B component, by weight, A component comprises 50 parts of polyaspartic acid esters, 35 parts of antirust base materials, 6 parts Parts of additive A and 12 parts of solvent A (MOCA), wherein the fineness of anti-rust base material is ≤25um, which includes 2.5 parts of pigment (rutile titanium dioxide), 7 parts of filler (1.4 parts of talc and 5.6 parts of barium sulfate) , 19 parts of polyaspartic acid ester, 2.5 parts of aluminum tripolyphosphate, 1.5 parts of zinc phosphate, 2.5 parts of dispersant (BYK2155), additive A includes 1.5 parts of defoamer (BYK1799) and 4.5 parts of UV absorber (1.5 Parts of Tinuvin 400 and 3 parts of Tinuvin246); The B component is a hydrophilic modified polyisocyanate, which includes 100 parts of HDI trimer (80 parts of HDI uretdione isocyanate and 40 parts of HDI trimer isocyanate), 2 parts Additive B (sulfonic acid monomer) and 3 parts of so...
PUM
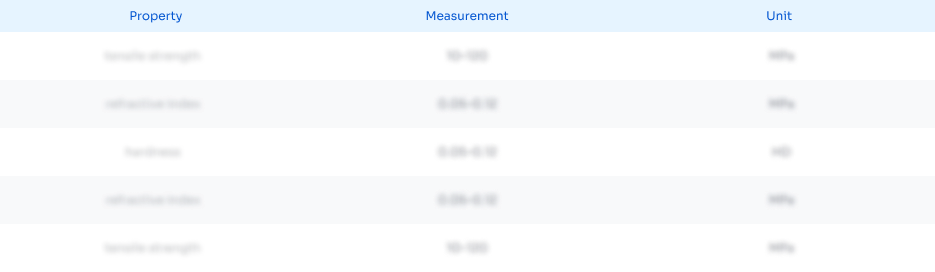
Abstract
Description
Claims
Application Information

- R&D
- Intellectual Property
- Life Sciences
- Materials
- Tech Scout
- Unparalleled Data Quality
- Higher Quality Content
- 60% Fewer Hallucinations
Browse by: Latest US Patents, China's latest patents, Technical Efficacy Thesaurus, Application Domain, Technology Topic, Popular Technical Reports.
© 2025 PatSnap. All rights reserved.Legal|Privacy policy|Modern Slavery Act Transparency Statement|Sitemap|About US| Contact US: help@patsnap.com