Dyeing method of blended fabric
A technology of blended fabrics and dyeing methods, applied in dyeing methods, textiles and papermaking, etc., can solve the problems of high temperature instability of direct dyes, difficulty in color matching, poor level dyeing and dyeing depth, etc., to achieve reduction of dyes and level dyeing The use of additives, saving cost and dyeing time, improving the effect of coloring effect
- Summary
- Abstract
- Description
- Claims
- Application Information
AI Technical Summary
Problems solved by technology
Method used
Image
Examples
Embodiment 1
[0029] The micro-denier polyester / viscose fiber (65 / 35) blended fabric was dyed by traditional dyeing process (two-bath method).
[0030] The components and dosage of dyeing materials are as follows:
[0031] Disperse dye black SW-VIP 3%, leveling agent 0.5g / L, glacial acetic acid 1g / L, hydrosulfite 3g / L, caustic soda 3g / L, reactive dye black WNN 5%, sodium sulfate 80g / L, sodium carbonate 20g / L, degreasing agent 1g / L, soaping agent 1g / L, color fixing agent 3g / L;
[0032] Wherein, disperse dye black SW-VIP is purchased from: Shanghai Yayun Chemical Co., Ltd., reactive dye black WNN is purchased from: Taixing Jinji Chemical Dyestuff Co., Ltd., leveling agent DL-200: Qingdao Guowei Textile Chemical Co., Ltd.; 85%): Yantai Jinhe Sodium Powder Factory Co., Ltd.; degreasing agent MRZ: Shanghai Argo Chemical Co., Ltd.; soaping agent SN: Shanghai Langsi Chemical Co., Ltd.; color fixing agent KY-R: Zhejiang Transfar Co., Ltd. .
[0033] The dyeing process is as follows:
[0034] (1...
Embodiment 2
[0047] The dyeing process of the invention is used to dye the micro-denier polyester / viscose fiber (65 / 35) blended fabric.
[0048] The components and dosage of dyeing materials are as follows:
[0049] New dye black CP-N 8%, Yuanming powder 100g / L, degreasing agent 1g / L, cleaning agent 1.5g / L, color fixing agent 3g / L.
[0050] Among them, the new dye black CP-N was purchased from: Shanghai Yayun Chemical Co., Ltd., the cleaning agent was purchased from: Qingdao Guowei Textile Chemical Co., Ltd., the degreasing agent MRZ was purchased from: Shanghai Argo Chemical Co., Ltd., the color fixing agent KY- R was purchased from: Zhejiang Transfar Co., Ltd.
[0051] The dyeing process is as follows:
[0052](1) One-bath dyeing of micro-denier polyester and viscose fiber
[0053] Add the micro-denier polyester / viscose fiber blended fabric and 35°C±2 water into the dyeing vat, control the bath ratio to 1:4.5, add degreasing agent to the dyeing vat in turn (take 10 minutes to add), ne...
Embodiment 3
[0061] Adopt dyeing process of the present invention to dye 50S single jersey (65%T / 35%R), the color code name of jersey is ZMHY-126 black, and fabric gram weight 150g / m 2 .
[0062] The components and dosage of dyeing materials are as follows:
[0063] New dye black CP-N 5%, Yuanming powder 100g / L, degreasing agent 1g / L, cleaning agent 1.5g / L, color fixing agent 3g / L.
[0064] Among them, the new dye black CP-N was purchased from: Shanghai Yayun Chemical Co., Ltd., the cleaning agent was purchased from: Qingdao Guowei Textile Chemical Co., Ltd., the degreasing agent MRZ was purchased from: Shanghai Argo Chemical Co., Ltd., the color fixing agent KY- R was purchased from: Zhejiang Transfar Co., Ltd.
[0065] The dyeing process is as follows:
[0066] (1) Dyeing
[0067] Add jersey and water at 35°C±2 to the dye vat, control the bath ratio to 1:4.5, add degreaser (completely added in 10 minutes), new dye black CP-N (completely added in 30 min) and yuan Staring powder (comp...
PUM
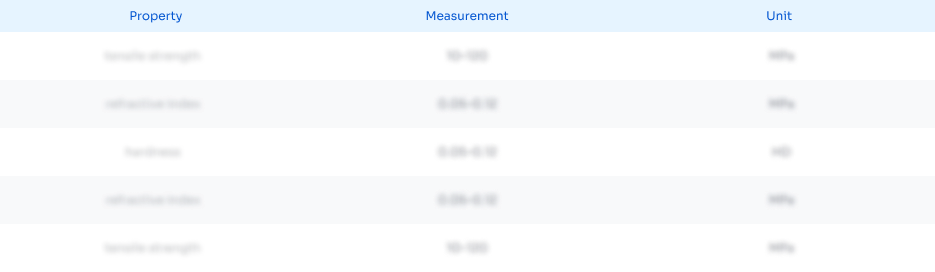
Abstract
Description
Claims
Application Information

- Generate Ideas
- Intellectual Property
- Life Sciences
- Materials
- Tech Scout
- Unparalleled Data Quality
- Higher Quality Content
- 60% Fewer Hallucinations
Browse by: Latest US Patents, China's latest patents, Technical Efficacy Thesaurus, Application Domain, Technology Topic, Popular Technical Reports.
© 2025 PatSnap. All rights reserved.Legal|Privacy policy|Modern Slavery Act Transparency Statement|Sitemap|About US| Contact US: help@patsnap.com