Production method of carbon black for green tire with high wear resistance and low rolling resistance
A technology for green tires and production methods, applied in fibrous fillers and other directions, can solve the problems of high mixing temperature, unreasonable design and high noise, and achieve the effects of increasing preheating temperature, improving atomization effect and sufficient cracking reaction
- Summary
- Abstract
- Description
- Claims
- Application Information
AI Technical Summary
Problems solved by technology
Method used
Image
Examples
Embodiment 1
[0038] A kind of production method of carbon black for green tire with high wear resistance and low rolling resistance,
[0039] Add boric acid to the anthracene oil and mix well to obtain the anthracene oil-boric acid mixture;
[0040] Preheat the anthracene oil boric acid mixture to 210°C;
[0041] Input air and gas into the combustion section of the reaction furnace, the volume ratio of air and gas is 15:1;
[0042] When the temperature of the combustion section is 2000°C, add the preheated anthracene oil boric acid mixture to the throat section of the reaction furnace;
[0043] The flue gas velocity generated in the combustion section is 190m / s;
[0044] The flow rate of the anthracene oil boric acid mixture is 4900kg / h, and the raw material is 2.8Mpa;
[0045] Spray cold water into the quenching section of the reaction furnace to terminate the anthracene oil reaction;
[0046] The reaction time of anthracene oil is 0.08s;
[0047] The mass ratio of anthracene oil to ...
Embodiment 2
[0063] A kind of production method of carbon black for green tire with high wear resistance and low rolling resistance,
[0064] Add boric acid to the anthracene oil and mix well to obtain the anthracene oil-boric acid mixture;
[0065] Preheat the anthracene oil boric acid mixture to 210°C;
[0066] Input air and gas into the combustion section of the reaction furnace, the volume ratio of air and gas is 15:1;
[0067] When the temperature of the combustion section is 1980°C, add the preheated anthracene oil boric acid mixture to the throat section of the reaction furnace;
[0068] The flue gas velocity generated in the combustion section is 200m / s;
[0069] The flow rate of the anthracene oil boric acid mixture is 4800kg / h, and the raw material is 2.8Mpa;
[0070] Spray cold water into the quenching section of the reaction furnace to terminate the anthracene oil reaction;
[0071] The reaction time of anthracene oil is 0.08s;
[0072] The mass ratio of anthracene oil to ...
Embodiment 3
[0088] A kind of production method of carbon black for green tire with high wear resistance and low rolling resistance,
[0089] Add boric acid to the anthracene oil and mix well to obtain the anthracene oil-boric acid mixture;
[0090] Preheat the anthracene oil boric acid mixture to 210°C;
[0091] Input air and gas into the combustion section of the reaction furnace, the volume ratio of air and gas is 15:1;
[0092] When the temperature of the combustion section is 1990°C, add the preheated anthracene oil boric acid mixture to the throat section of the reaction furnace;
[0093] The flue gas velocity generated in the combustion section is 200m / s;
[0094] The flow rate of anthracene oil boric acid mixture is 5100kg / h, and the raw material is 3.0Mpa;
[0095] Spray cold water into the quenching section of the reaction furnace to terminate the anthracene oil reaction;
[0096] The reaction time of anthracene oil is 0.09s;
[0097] The mass ratio of anthracene oil to bori...
PUM
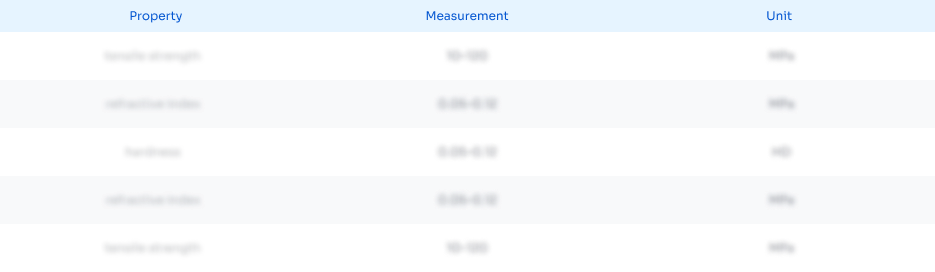
Abstract
Description
Claims
Application Information

- Generate Ideas
- Intellectual Property
- Life Sciences
- Materials
- Tech Scout
- Unparalleled Data Quality
- Higher Quality Content
- 60% Fewer Hallucinations
Browse by: Latest US Patents, China's latest patents, Technical Efficacy Thesaurus, Application Domain, Technology Topic, Popular Technical Reports.
© 2025 PatSnap. All rights reserved.Legal|Privacy policy|Modern Slavery Act Transparency Statement|Sitemap|About US| Contact US: help@patsnap.com