Method for magnetizing and roasting iron tailings through biomass
A technology of magnetization roasting and biomass, which is applied in the field of solid waste resource utilization, can solve the problem that the recovery rate and grade of iron tailings cannot be taken into account at the same time, so as to reduce the emission of pollutants such as SO2 and NOx, and reduce the emission of CO2 , to achieve the effect of high-speed rail recovery
- Summary
- Abstract
- Description
- Claims
- Application Information
AI Technical Summary
Problems solved by technology
Method used
Image
Examples
Embodiment 1
[0054] Embodiment 1 A kind of method of biomass magnetization roasting iron tailings
[0055] S1. Dry the iron tailings in a blast drying oven at 105°C for 24 hours, crush them after cooling, and then grind them to -0.074mm (through a 200-mesh sieve) with a planetary ball mill to obtain iron tailings powder;
[0056] S2. Dry the eucalyptus wood in a forced air drying oven at 105°C for 24 hours, and after cooling, crush it to -0.15mm in a crusher (passing through a 100-mesh sieve) to obtain eucalyptus wood chips;
[0057] S3. Introduce nitrogen into the tube furnace to replace the air in the furnace chamber and its connection. At the same time, set two gas washing bottles at the gas outlet. One washing bottle is filled with water to prevent air from being sucked back in, and the other is left empty to prevent the cooling process. Reclaimed water is sucked back into the tube furnace; 10g of iron tailings powder and 1.5g of eucalyptus wood chips are placed on two porcelain boats re...
Embodiment 2
[0059] Embodiment 2 A kind of method of biomass magnetization roasting iron tailings
[0060] With the method of Example 1, the difference is that step S2 uses pine instead of eucalyptus; step S3 uses 1 g of pine chips.
Embodiment 3
[0061] Embodiment 3 A kind of method of biomass magnetization roasting iron tailings
[0062] The same as the method in Example 1, the difference is that in step S2, fir is used instead of eucalyptus; in step S3, the amount of fir chips is 2.5g; in step S4, the magnetic induction of wet magnetic separation is 0.2T.
PUM
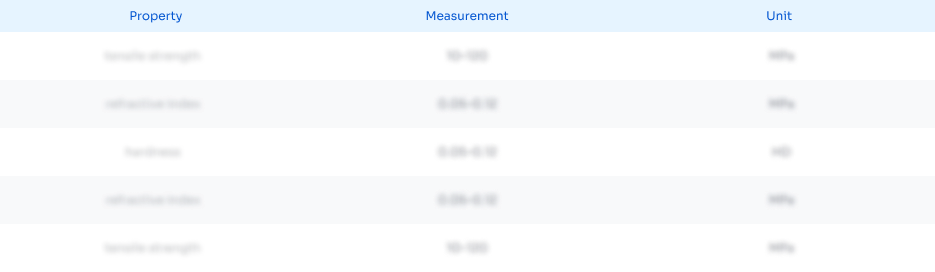
Abstract
Description
Claims
Application Information

- Generate Ideas
- Intellectual Property
- Life Sciences
- Materials
- Tech Scout
- Unparalleled Data Quality
- Higher Quality Content
- 60% Fewer Hallucinations
Browse by: Latest US Patents, China's latest patents, Technical Efficacy Thesaurus, Application Domain, Technology Topic, Popular Technical Reports.
© 2025 PatSnap. All rights reserved.Legal|Privacy policy|Modern Slavery Act Transparency Statement|Sitemap|About US| Contact US: help@patsnap.com