Method for separating and recovering selenium and mercury in acid mud through one-step method
A technology for separation and recovery of acid sludge, applied in the direction of element selenium/tellurium, improvement of process efficiency, binary selenium/tellurium compounds, etc., can solve the problems of difficult separation of selenium and mercury, complicated technical process, etc., and achieve short mercury separation process , high safety release control, high separation efficiency
- Summary
- Abstract
- Description
- Claims
- Application Information
AI Technical Summary
Problems solved by technology
Method used
Image
Examples
Embodiment 1
[0025] Embodiment 1: the method (see figure 1 ),Specific steps are as follows:
[0026] (1) Slurry: Mix the acid mud with the slurry liquid and slurry at a temperature of 25°C for 120 minutes to obtain a slurry; wherein the mass content of mercury in the dried acid mud is 1%, the mass content of selenium is 1%, and the acid mud The solid-to-liquid ratio g:mL of the slurry is 1:6, the slurry contains hydrochloric acid and oxidant (potassium permanganate), the concentration of hydrochloric acid in the slurry is 20g / L, and the concentration of oxidant in the slurry is 2g / L;
[0027] (2) Roasting: put the slurry in step (1) at a temperature of 400°C and microwave in an air atmosphere for 20 minutes to obtain Hg and SeO 2 The mixed steam and roasting slag, the total content of mercury and selenium in the roasting slag does not exceed 1%, and the roasting slag is used for recovery of valuable metals in pyrometallurgy; the flow rate of air is 1L / min;
[0028] (3) Mercury recovery...
Embodiment 2
[0032] Embodiment 2: the method (see figure 1 ),Specific steps are as follows:
[0033] (1) Slurry: mix the acid mud with the slurry liquid and slurry at a temperature of 60°C for 60 minutes to obtain a slurry; wherein the mass content of mercury in the dried acid mud is 43%, the mass content of selenium is 8%, and the acid mud The solid-liquid ratio g:mL with the slurrying liquid is 2:1, sulfuric acid and oxidant (hydrogen peroxide) are contained in the slurrying liquid, the concentration of sulfuric acid in the slurrying liquid is 90g / L, and the concentration of oxidant in the slurrying liquid is 35g / L;
[0034] (2) Roasting: put the slurry in step (1) at a temperature of 600°C and microwave in an air atmosphere for 60 minutes to obtain Hg and SeO 2 The mixed steam and roasting slag, the total content of mercury and selenium in the roasting slag does not exceed 1%, and the roasting slag is used for recovery of valuable metals in pyrometallurgy; the flow rate of air is 10L / m...
Embodiment 3
[0038] Embodiment 3: the method (see figure 1 ),Specific steps are as follows:
[0039](1) Slurry: mix the acid mud with the slurry liquid and slurry at a temperature of 90°C for 100 minutes to obtain a slurry; wherein the mass content of mercury in the dried acid mud is 9%, the mass content of selenium is 71%, and the acid mud The solid-to-liquid ratio g:mL of the slurry is 6:1, the slurry contains nitric acid and oxidant (hypochlorous acid), the concentration of nitric acid in the slurry is 200g / L, and the concentration of oxidant in the slurry is 100g / L L;
[0040] (2) Roasting: Put the slurry in step (1) at a temperature of 800°C and microwave in an air atmosphere for 120 minutes to obtain Hg and SeO 2 The mixed steam and roasting slag, the total content of mercury and selenium in the roasting slag does not exceed 1%, and the roasting slag is used for recovery of valuable metals in pyrometallurgy; the flow rate of air is 10L / min;
[0041] (3) Mercury recovery by condens...
PUM
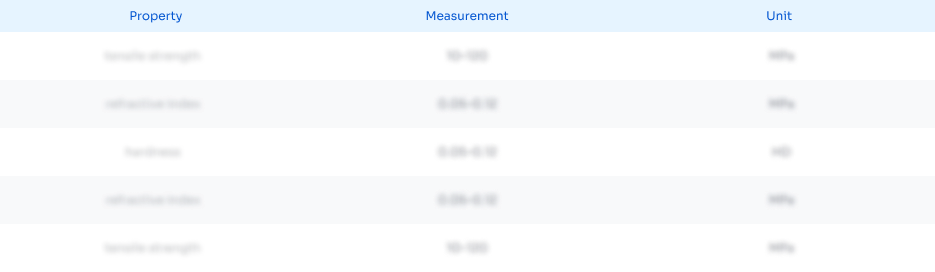
Abstract
Description
Claims
Application Information

- R&D Engineer
- R&D Manager
- IP Professional
- Industry Leading Data Capabilities
- Powerful AI technology
- Patent DNA Extraction
Browse by: Latest US Patents, China's latest patents, Technical Efficacy Thesaurus, Application Domain, Technology Topic, Popular Technical Reports.
© 2024 PatSnap. All rights reserved.Legal|Privacy policy|Modern Slavery Act Transparency Statement|Sitemap|About US| Contact US: help@patsnap.com