Method for alloying ultra-low carbon and degassed steel titanium in RH furnace
An ultra-low carbon, titanium alloy technology, used in the manufacture of converters and other directions, can solve the problems of overoxidation of molten steel at the end, high nitrogen content of the molten steel at the end, and insufficient temperature at the end of the converter, so as to achieve stable and controlled nitrogen content, small fluctuation range, The effect of meeting process quality control requirements
- Summary
- Abstract
- Description
- Claims
- Application Information
AI Technical Summary
Problems solved by technology
Method used
Examples
Embodiment 1
[0046] Pangang Group Xichang Steel and Vanadium Co., Ltd. steelworks smelting ultra-low carbon phosphorus-strengthened high-manganese steel for a furnace, RH arrival station molten steel temperature 1630-1640℃, [C]%: 0.02%-0.05%, [O] in the steel 500~600ppm, after LD blowing, LF furnace process temperature and rhythm adjustment, enter the RH furnace process for treatment, the service life of the RH vacuum chamber insertion tube is in the early and mid-term, and the service life (use times) ≤ 50 times (cumulative use time ≤ 1000 minutes) The RH treatment time of this steel type is about 31 minutes per furnace; the specific control situation: when the steel type RH molten steel is treated with phosphorus-ferroalloy and manganese-ferroalloy for phosphorus and manganese alloying, and the decarburization treatment cycle time lasts to about At 16-18 minutes (final decarburization), measure the temperature and oxygen of the molten steel, add aluminum particles for final deoxidation al...
Embodiment 2
[0048] Xichang Steel and Vanadium Co., Ltd. of Panzhihua Iron and Steel Group smelted a furnace of IF series ultra-low carbon steel. The temperature of molten steel at the RH station was 1630~1650℃, [C]%: 0.03%~0.04%, and [O] in steel was 500~ 700ppm, after LD blowing, LF furnace process temperature and rhythm adjustment, it is processed in RH furnace process, the service life of the RH vacuum chamber insertion tube is in the early and mid-term, and the service life (use times) ≤ 50 times (cumulative use time ≤ 1000 minutes), The RH treatment time of this steel type is about 31 minutes per furnace; the specific control situation: when the steel type RH molten steel is treated with ferromanganese alloy for manganese alloying, and the decarburization treatment cycle time lasts to about 16-18 minutes ( Decarburization final), at this time, temperature measurement and oxygen determination are performed on molten steel, and aluminum particles are added for final deoxidation alloying...
PUM
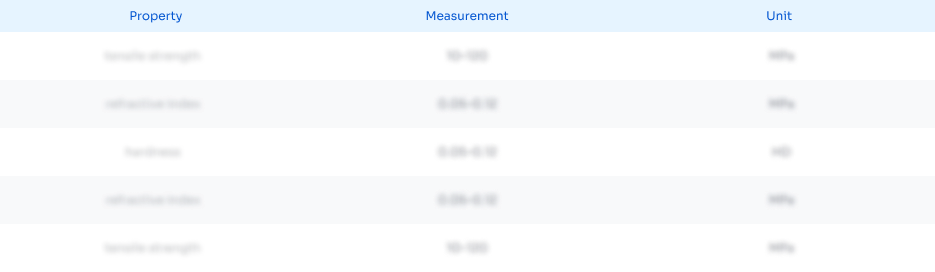
Abstract
Description
Claims
Application Information

- R&D
- Intellectual Property
- Life Sciences
- Materials
- Tech Scout
- Unparalleled Data Quality
- Higher Quality Content
- 60% Fewer Hallucinations
Browse by: Latest US Patents, China's latest patents, Technical Efficacy Thesaurus, Application Domain, Technology Topic, Popular Technical Reports.
© 2025 PatSnap. All rights reserved.Legal|Privacy policy|Modern Slavery Act Transparency Statement|Sitemap|About US| Contact US: help@patsnap.com