Method for controlling nitrogen content of niobium-containing steel type
A control method and technology of nitrogen content, applied in the manufacture of converters, etc., can solve the problems of continuous casting slab hot charging and hot delivery, molten steel nitrogen absorption, large alloy amount, etc., to avoid excessive nitrogen content, improve heat delivery rate, The effect of reducing nitrogen addition
- Summary
- Abstract
- Description
- Claims
- Application Information
AI Technical Summary
Problems solved by technology
Method used
Image
Examples
Embodiment 1
[0036] Melting number 16BD1610, steel code A400LF, converter end point temperature 1687°C, oxygen value 658ppm, no supplementary oxygen blowing, converter end point comprehensive oxygen value 658ppm, argon blowing time for ladle before tapping is 2min, argon blowing flow rate is 80Nm 3 / h. Add 1.43 tons of alloy silicon-manganese, 2.29 tons of medium-carbon ferromanganese, and 0.2 tons of aluminum-manganese ferromanganese, and blow argon for 3 minutes when the tapping amount reaches one-third of the ladle, and the flow rate of argon blowing is 80Nm 3 / h. After tapping, the ladle was transported to the argon station for sampling and sent to the laboratory for testing. The nitrogen content in the molten steel was 19ppm.
Embodiment 2
[0038] Melting number 16CD1526, steel code L450M, converter end point temperature 1677°C, oxygen value 705ppm, supplemental oxygen blowing for 20 seconds, converter end point comprehensive oxygen value 905ppm, argon blowing time for ladle before tapping, 4min, argon blowing flow rate 80Nm 3 / h. Add 0.82 tons of alloy silicon manganese, 1.97 tons of medium carbon ferromanganese, and 0.17 tons of aluminum manganese ferromanganese, and blow argon for 2 minutes when the tapping amount reaches one third of the ladle, and the flow rate of argon blowing is 80Nm 3 / h. After tapping, the ladle was transported to the argon station for sampling and sent to the laboratory for testing. The nitrogen content in the molten steel was 23ppm.
PUM
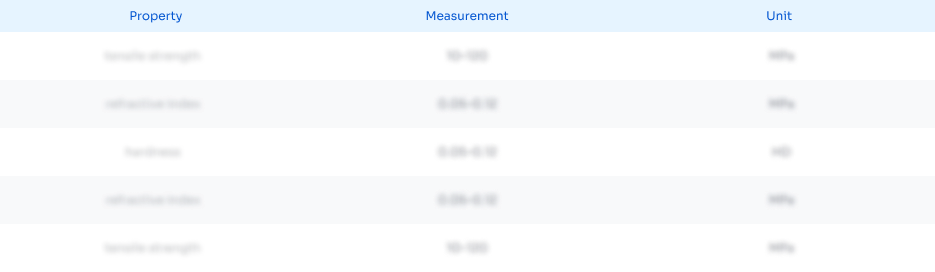
Abstract
Description
Claims
Application Information

- R&D Engineer
- R&D Manager
- IP Professional
- Industry Leading Data Capabilities
- Powerful AI technology
- Patent DNA Extraction
Browse by: Latest US Patents, China's latest patents, Technical Efficacy Thesaurus, Application Domain, Technology Topic, Popular Technical Reports.
© 2024 PatSnap. All rights reserved.Legal|Privacy policy|Modern Slavery Act Transparency Statement|Sitemap|About US| Contact US: help@patsnap.com