A kind of method for adjusting carbon by LF refining for carbon steel
A carbon steel and carbon adjustment technology, which is applied in the field of LF refining and carbon adjustment for carbon steel, can solve the problems of increasing the difficulty of precise control of components, uneven composition of molten steel, slag hanging on the furnace cover and ladle car, etc. Argon stirring time, reduction of argon consumption, effect of carbon composition control
- Summary
- Abstract
- Description
- Claims
- Application Information
AI Technical Summary
Problems solved by technology
Method used
Examples
Embodiment 1
[0031] For steel type J55, the sulfur content of a certain can was higher than the upper limit of the finished product by 0.001%, and the carbon content was lower than the lower limit of the finished product by 0.06%.
[0032] The specific implementation steps are as follows:
[0033] 1. Add carburant 0.75kg / ton of steel, increase the argon flow to 500Nl / min for large argon stirring.
[0034] 2. After stirring for 25 seconds, the recarburizer is covered by molten slag. Reduce the argon gas flow rate to 260NL / min to heat and melt the carburant agent. After heating for 5.8 minutes, the carburant agent is completely melted. Stop heating and adjust the argon gas flow rate. Stir again at a maximum of 450 NL / min.
[0035] 3. After stirring for 24 seconds, the composition of the molten steel is completely uniform, and the molten steel sample is taken and sent to the laboratory for inspection. The test results show that the carbon and sulfur components all meet the composition requi...
Embodiment 2
[0037] For steel type 45#, the sulfur content of a certain can was higher than the upper limit of the finished product by 0.002%, and the carbon content was lower than the lower limit of the finished product by 0.055%.
[0038] The specific implementation steps are as follows:
[0039] 1. Add carburant 0.7kg / ton of steel, increase the argon flow rate to 450NL / min for large argon stirring;
[0040] 2. After stirring for 22 seconds, the recarburizer is covered by slag. Reduce the argon gas flow rate to 240NL / min to add the molten recarburizer. After heating for 5.6 minutes, the carburant agent is completely melted, stop adding and reduce the argon flow rate Turn up to 480NL / min and stir again;
[0041] 3. After stirring for 20 seconds, the composition of the molten steel is completely uniform, and the molten steel sample is taken and sent to the laboratory for inspection. The test results show that the carbon and sulfur components all meet the composition requirements of the f...
PUM
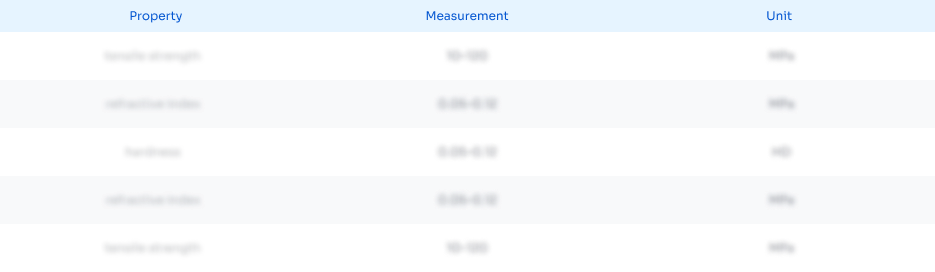
Abstract
Description
Claims
Application Information

- R&D
- Intellectual Property
- Life Sciences
- Materials
- Tech Scout
- Unparalleled Data Quality
- Higher Quality Content
- 60% Fewer Hallucinations
Browse by: Latest US Patents, China's latest patents, Technical Efficacy Thesaurus, Application Domain, Technology Topic, Popular Technical Reports.
© 2025 PatSnap. All rights reserved.Legal|Privacy policy|Modern Slavery Act Transparency Statement|Sitemap|About US| Contact US: help@patsnap.com