Conductive film gas separation type etching process
A conductive film and separation technology, applied in the field of conductive film gas separation etching process, can solve the problems of increased peeling difficulty, difficult to effectively peel off, conductive line damage, etc., to achieve the effect of not easy residual phenomenon, easy peeling, and avoiding damage
- Summary
- Abstract
- Description
- Claims
- Application Information
AI Technical Summary
Problems solved by technology
Method used
Image
Examples
Embodiment 1
[0044] see figure 1 , a conductive film gas ion etching process, comprising the following steps:
[0045] S1. Prepare the etching ink in advance according to the material of the conductive film, and then disperse, grind and filter in turn for later use;
[0046] S2, coating the etching ink on the conductive film, and then taking a plurality of air ionized microspheres and embedding them in the etching ink;
[0047] S3, intermittently applying a magnetic field on the back of the conductive film, forcing the gas-separated microspheres to intermittently squeeze the etching ink, so that the etching ink is fully in contact with the conductive film for etching;
[0048] S4. After the etching is completed, the magnetic field is withdrawn, and then heating and drying are performed, and at the same time, the action of releasing the gas from the aerosol microspheres is triggered, so that the gas is filled into the gap to facilitate the peeling of the etching ink;
[0049] S5. After th...
Embodiment 2
[0059] see Image 6 The upper side of the hollow ink press ball 1 is provided with a cover ink scale 4, and there are multiple evenly distributed elastic drawing wires 5 connected between the ink cover scale 4 and the hollow ink press ball 1, and the etching ink can be covered by the ink cover scale 4, Utilize the integrality of cover ink scale 4, when film is peeled off, it is difficult to appear the phenomenon that single point is stressed excessively and excessive bending cracks, and when hollow ink ball 1 moves up and down under the effect of intermittent magnetic field, also can Acting on the ink covering scale 4 to squeeze the etching ink as a whole, the etching effect is better, and the peeling effect of the film can also be improved by utilizing the bonding force between the film and the ink covering scale 4 during peeling.
[0060] The present invention can mix a plurality of air ionized microspheres into the etching ink, and intermittently apply a magnetic field unde...
PUM
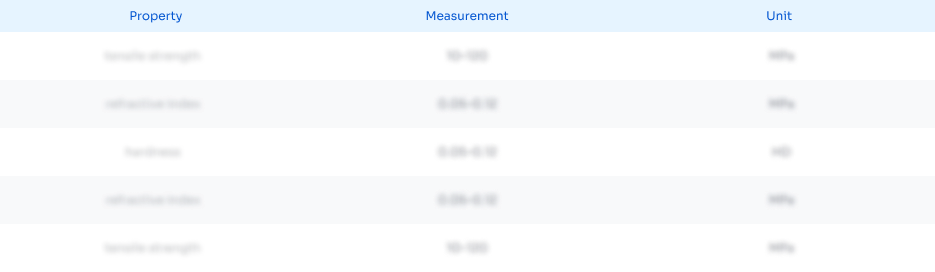
Abstract
Description
Claims
Application Information

- R&D
- Intellectual Property
- Life Sciences
- Materials
- Tech Scout
- Unparalleled Data Quality
- Higher Quality Content
- 60% Fewer Hallucinations
Browse by: Latest US Patents, China's latest patents, Technical Efficacy Thesaurus, Application Domain, Technology Topic, Popular Technical Reports.
© 2025 PatSnap. All rights reserved.Legal|Privacy policy|Modern Slavery Act Transparency Statement|Sitemap|About US| Contact US: help@patsnap.com