Polypropylene melt-blown non-woven fabric based on composite antibacterial electret master batches and preparation method
A polypropylene melt-blown and composite antibacterial technology, which is applied in the manufacture of non-woven fabrics, single-component polyolefin rayon, rayon, etc., can solve the problem of increasing the fiber diameter and pores of polypropylene non-woven fabrics, polypropylene melt The antibacterial effect of spray cloth is short-lived and the filtration performance is reduced, so as to achieve the effects of excellent high efficiency and low resistance performance, enhanced antibacterial performance, long-lasting charge storage capacity, and enhanced antibacterial performance
- Summary
- Abstract
- Description
- Claims
- Application Information
AI Technical Summary
Problems solved by technology
Method used
Image
Examples
preparation example Construction
[0033] The invention provides a method for preparing a polypropylene melt-blown nonwoven fabric based on a composite antibacterial electret masterbatch, comprising the following steps:
[0034] S1, preparation of antibacterial masterbatch: After fully mixing polypropylene wax-grafted maleic anhydride masterbatch, polyhexamethyleneguanidine hydrochloride and conventional polypropylene masterbatch according to a predetermined ratio, extrusion granulation was carried out to prepare Obtain polypropylene wax grafted polyhexamethylene guanidine hydrochloride antibacterial masterbatch;
[0035] S2. Preparation of composite antibacterial electret masterbatch: After washing and drying the antibacterial masterbatch prepared in step S1, immerse in the silane coupling agent mixture, stir for 10-20min, and then add a predetermined amount of nano grade silicon dioxide, fully stirred, and then dried and cured to prepare a composite antibacterial electret masterbatch;
[0036] S3, the prepar...
Embodiment 1
[0047] S1. Preparation of antibacterial masterbatch: After fully mixing polypropylene wax-grafted maleic anhydride masterbatch, polyhexamethyleneguanidine hydrochloride and conventional polypropylene masterbatch at a ratio of 15:3:5, the main feed The feed port is fed into a twin-screw extruder, and then the extruded product is pelletized to obtain the antibacterial masterbatch of polypropylene wax-grafted polyhexamethyleneguanidine hydrochloride.
[0048] Wherein, the grafting rate of the polypropylene wax grafted with maleic anhydride is 6% to 8%; the twin-screw extruder contains 9 heating sections, from the feed to the machine head, the set section temperature Incremental in turn, the temperature setting range is 140-180°C, the main screw motor speed is 40rpm, the main feeding motor speed is 15rpm, and the specific temperature of the 9 heating sections is set as: 140°C, 150°C, 160°C, 160°C ℃, 165℃, 170℃, 170℃, 175℃, 180℃.
[0049] S2, silicon dioxide (SiO 2 ) Modified com...
Embodiment 2-7
[0067] The difference from Example 1 is that the proportioning of each raw material in the preparation process is different, as shown in Table 1, and the others are the same as in Example 1, and will not be repeated here.
[0068] Table 1 is each raw material ratio setting and its performance parameter in embodiment 1-7 and comparative example 1-2
[0069]
[0070] Combined with Table 1 for analysis:
[0071] 1) The effect of the ratio setting of polypropylene wax grafted maleic anhydride masterbatch, polyhexamethyleneguanidine hydrochloride and conventional polypropylene masterbatch on the properties of polypropylene meltblown nonwovens is: polypropylene wax and The proportion of polyhexamethyleneguanidine hydrochloride will affect the grafting rate and antibacterial effect between the two; the proportion of conventional polypropylene masterbatch will affect whether the final extruded melt can be granulated, and its proportion is too low. If the melt viscosity is too high...
PUM
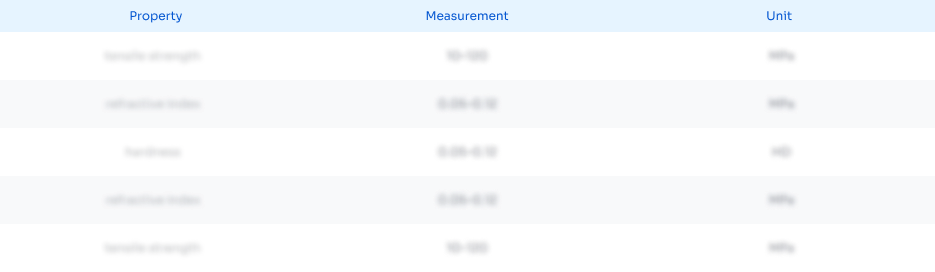
Abstract
Description
Claims
Application Information

- R&D Engineer
- R&D Manager
- IP Professional
- Industry Leading Data Capabilities
- Powerful AI technology
- Patent DNA Extraction
Browse by: Latest US Patents, China's latest patents, Technical Efficacy Thesaurus, Application Domain, Technology Topic, Popular Technical Reports.
© 2024 PatSnap. All rights reserved.Legal|Privacy policy|Modern Slavery Act Transparency Statement|Sitemap|About US| Contact US: help@patsnap.com