Method for removing ethyl dichlorosilane impurities in dimethyldichlorosilane
A technology of dimethyldichlorosilane and ethyldichlorosilane is applied in the separation and purification field of the organosilicon industry, and can solve the problems of high energy consumption, large reflux ratio and high number of trays
- Summary
- Abstract
- Description
- Claims
- Application Information
AI Technical Summary
Problems solved by technology
Method used
Image
Examples
Embodiment 1
[0044] The content of ethyldichlorosilane in the feed is 1000ppm, and ethylene is used as the reactant for the reaction, and the isopropanol solution of chloroplatinic acid hydrate is used as the catalyst, and the catalyst concentration is 15ppm. The reactor is a stirred tank reactor with a reaction volume of 5 L, an operating pressure of 0.1 MPaG, and a reaction temperature of 90°C. Control the molar ratio of the circulating amount of reactants to dimethyldichlorosilane to be 8:1, the reaction residence time is 0.2 hours, and the reaction kettle has a jacket, external circulation or internal coil heater. Adjust the amount of heating to stabilize the liquid level of the reactor, add the reactants continuously, and the reaction products enter the rectification system. After delightening, the light component ethylene returns to the reactor in the gas phase, and the remaining mixture of dimethyldichlorosilane and diethyldichlorosilane is refined to obtain dimethyldichlorosilane p...
Embodiment 2
[0050] In this example, acetylene is used as the hydrosilylation reactant, and the content of ethyldichlorosilane in the feed is 1000ppm. The process is similar to the use of ethylene. The isopropanol solution of chloroplatinic acid hydrate is used as the catalyst, and the catalyst concentration is 150ppm. The reactor is a stirred tank reactor with a reaction volume of 5 L, an operating pressure of 0 MPaG, and a reaction temperature of 120°C. Control the molar ratio of the circulating amount of reactants to dimethyldichlorosilane to be 8:1, the reaction residence time is 1 hour, and the reaction kettle has a jacket, external circulation or internal coil heater. Adjust the amount of heating to stabilize the liquid level of the reactor, add the reactants continuously, and the reaction products enter the rectification system. After delighting, the light component acetylene returns to the reactor in the gas phase, and the remaining dimethyldichlorosilane, ethylvinyldichlorosilane ...
Embodiment 3
[0058] The content of ethyldichlorosilane in the feed is 1000ppm, and 1-octene is used as a reactant for the reaction, and a Karstedt catalyst is used with a catalyst concentration of 10ppm. The reactor is a stirred tank reactor with a reaction volume of 5 L, an operating pressure of 1.0 MPaG, and a reaction temperature of 120°C. Control the molar ratio of the circulating amount of reactants to dimethyldichlorosilane to 3:1, the reaction residence time is 0.1 hour, and the reaction kettle has a jacket, external circulation or internal coil heater. Adjust the amount of heating to stabilize the liquid level of the reactor, add the reactants continuously, and the reaction products enter the rectification system. A small amount of light component impurities are recovered after delightening, and then the dimethyldichlorosilane product is obtained after delightening treatment. 1-octene and ethyloctyldichlorosilane continue to be rectified and separated as heavy components, respectiv...
PUM
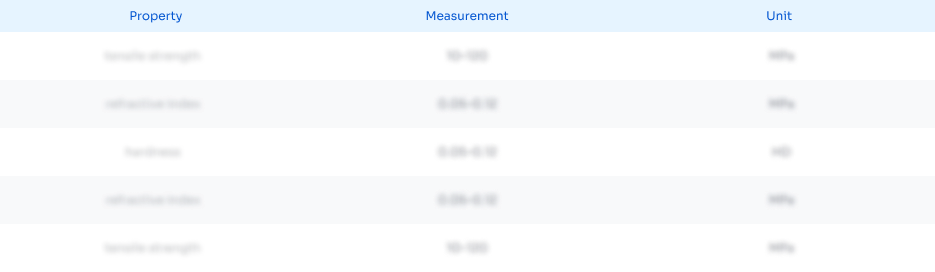
Abstract
Description
Claims
Application Information

- R&D
- Intellectual Property
- Life Sciences
- Materials
- Tech Scout
- Unparalleled Data Quality
- Higher Quality Content
- 60% Fewer Hallucinations
Browse by: Latest US Patents, China's latest patents, Technical Efficacy Thesaurus, Application Domain, Technology Topic, Popular Technical Reports.
© 2025 PatSnap. All rights reserved.Legal|Privacy policy|Modern Slavery Act Transparency Statement|Sitemap|About US| Contact US: help@patsnap.com