High-abundance rare earth sintered permanent magnet and preparation method thereof
A permanent magnet, high-abundance technology, used in the manufacture of magnetic objects, permanent magnets, inductors/transformers/magnets, etc., can solve the problems of poor consistency of cooling links, uneven sintering temperature, affecting product quality, etc., to improve product performance. , avoid grain growth, improve the effect of consistency
- Summary
- Abstract
- Description
- Claims
- Application Information
AI Technical Summary
Problems solved by technology
Method used
Image
Examples
no. 1 example
[0028] This embodiment provides a method for preparing a high-abundance rare earth permanent magnet, comprising the following steps:
[0029] 1. Obtain metal raw materials according to the ratio of 0.9-1.12% of boron-iron alloy, 64.38-70.1% of pure iron, 29-32.5% of rare earth elements, and 0-2% of trace elements; pretreatment removes oxidized impurities on the surface.
[0030] 2. Smelt and process the alloy obtained from the above pretreatment, put it into the melting furnace, evacuate to below 0.4Pa, preheat for 20-30min, and fill it with 2.7×10 4 Pa, followed by high-power smelting, the melting temperature is 1300-1380°C and the melting time is 25-35min.
[0031] 3. Pour the refined alloy solution into the mullite tundish, cool and cast through the circulating water-cooled barrel roll, and finally cool it in the water-cooled plate. When cooling, 0.03MPa argon gas is introduced to supplement the air for cooling; the surface speed of the copper roller is required to be cont...
Embodiment 2
[0043] This embodiment provides a high-abundance rare earth sintered permanent magnet, which includes the following elements in proportion by mass: 0.92% of boron-iron alloy, 66.58% of pure iron, 31.5% of rare earth elements, and 1% of trace elements.
[0044] Wherein, the rare earth elements include 75% praseodymium-neodymium alloy, 5% gadolinium-iron alloy and 20% high-abundance cerium according to the mass ratio. The trace elements are one or more of gallium, cobalt, aluminum, copper, zirconium, niobium and manganese.
[0045] Refer to Example 1 for the preparation process of the above-mentioned permanent magnet, and its sintering process parameters are set as follows.
[0046] Degassing and dehydrogenation: in a vacuum environment, control the temperature at 500°C and keep it warm for 2 hours;
[0047] Secondary degassing: control the temperature at 800°C and keep it warm for 4 hours;
[0048] High-temperature sintering: control the temperature at 900°C and keep it warm ...
Embodiment 3
[0051] This embodiment provides a high-abundance rare earth sintered permanent magnet, which includes the following elements in proportion by mass: 0.98% of boron-iron alloy, 66.02% of pure iron, 31.8% of rare earth elements, and 1.2% of trace elements.
[0052] Wherein, the rare earth elements include 50% praseodymium-neodymium alloy, 10% gadolinium-iron alloy and 40% high-abundance cerium according to the mass ratio. The trace elements are one or more of gallium, cobalt, aluminum, copper, zirconium, niobium and manganese.
[0053] Refer to Example 1 for the preparation process of the above-mentioned permanent magnet, and its sintering process parameters are set as follows.
[0054] Degassing and dehydrogenation: In a vacuum environment, control the temperature at 530°C and keep it warm for 1.5 hours;
[0055] Secondary degassing: control the temperature at 820°C and keep it warm for 3 hours;
[0056] High-temperature sintering: control the temperature at 950°C and keep it wa...
PUM
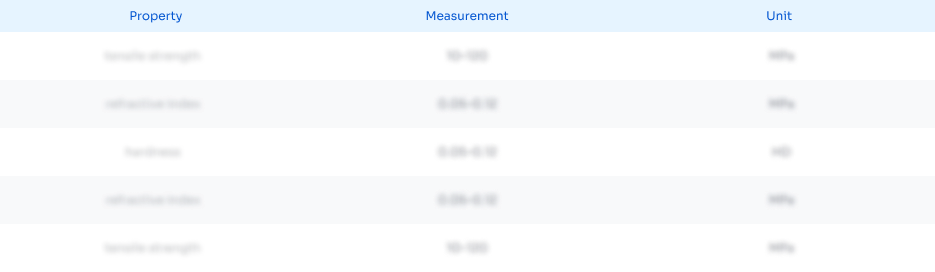
Abstract
Description
Claims
Application Information

- R&D Engineer
- R&D Manager
- IP Professional
- Industry Leading Data Capabilities
- Powerful AI technology
- Patent DNA Extraction
Browse by: Latest US Patents, China's latest patents, Technical Efficacy Thesaurus, Application Domain, Technology Topic, Popular Technical Reports.
© 2024 PatSnap. All rights reserved.Legal|Privacy policy|Modern Slavery Act Transparency Statement|Sitemap|About US| Contact US: help@patsnap.com