Preparation method and application of carbon-coated zinc diphosphide composite material prepared by three-step method
A technology of carbon-coated zinc diphosphide and composite materials, which is applied in the field of composite materials, can solve the problems of complexity, long cycle of metal phosphide preparation methods, and unsuitability for large-scale production, and achieve low preparation cost, excellent rate performance, The effect of high specific capacity
- Summary
- Abstract
- Description
- Claims
- Application Information
AI Technical Summary
Problems solved by technology
Method used
Image
Examples
Embodiment 1
[0039] A method for preparing a carbon-coated zinc diphosphide composite material, the specific operation steps are as follows:
[0040] Take a zinc block with a volume of 3cm*3cm*3cm and put it into the copper crucible of the DC arc plasma equipment, adjust the distance between the tungsten rod and the zinc block to 2cm, close the door and seal it. Use a combination of a mechanical pump and a molecular pump to evacuate the chamber to -0.1MPa, and then fill it with a mixture of 0.03MPa argon and 0.01MPa hydrogen. After arcing, adjust the working current of the equipment to 60A and the working voltage to 15V. After the zinc block is fully evaporated and collides with the argon molecules in the chamber, the energy of the zinc atoms will be lost and cooled to nucleate and grow to form a powder, which is deposited on the inner wall of the water-cooled reaction chamber and pass a certain amount of air to passivate it. Finally, air is filled to normal pressure to collect zinc nanop...
Embodiment 2
[0045] A method for preparing a carbon-coated zinc diphosphide composite material, the specific operation steps are as follows:
[0046] Take a 4cm*3cm*4cm zinc block and put it into the copper crucible of the DC arc plasma equipment, adjust the distance between the tungsten rod and the zinc block to 3cm, close the door and seal it. Use a combination of a mechanical pump and a molecular pump to evacuate the chamber to -0.1MPa, and then fill it with a mixture of 0.03MPa argon and 0.01MPa hydrogen. After arcing, adjust the working current of the equipment to 70A and the working voltage to 20V. After the zinc block is fully evaporated and collides with the argon molecules in the chamber, the energy of the zinc atoms will be lost and cooled to nucleate and grow to form a powder, which is deposited on the inner wall of the water-cooled reaction chamber and pass a certain amount of air to passivate it. Finally, air is filled to normal pressure to collect zinc nanopowder.
[0047] ...
Embodiment 3
[0051] A method for preparing a carbon-coated zinc diphosphide composite material, the specific operation steps are as follows:
[0052] Take a 2cm*2cm*2cm zinc block and put it into the copper crucible of the DC arc plasma equipment, adjust the distance between the tungsten rod and the zinc block to 4cm, close the door and seal it. Use a combination of a mechanical pump and a molecular pump to evacuate the chamber to -0.1MPa, and then fill it with a mixture of 0.03MPa argon and 0.01MPa hydrogen. After arcing, adjust the working current of the equipment to 80A and the working voltage to 15V. After the zinc block is fully evaporated and collides with the argon molecules in the chamber, the energy of the zinc atoms will be lost and cooled to nucleate and grow to form a powder, which is deposited on the inner wall of the water-cooled reaction chamber and pass a certain amount of air to passivate it. Finally, air is filled to normal pressure to collect zinc nanopowder.
[0053] ...
PUM
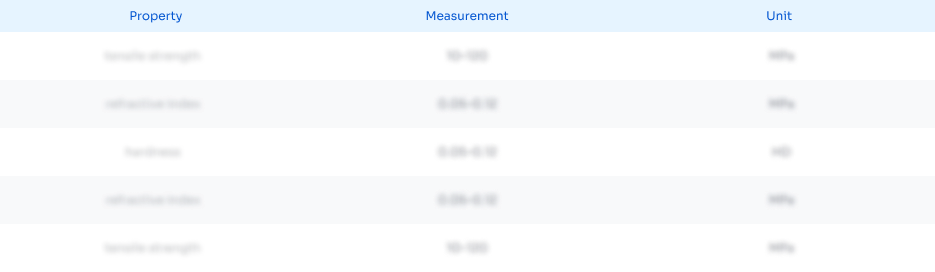
Abstract
Description
Claims
Application Information

- Generate Ideas
- Intellectual Property
- Life Sciences
- Materials
- Tech Scout
- Unparalleled Data Quality
- Higher Quality Content
- 60% Fewer Hallucinations
Browse by: Latest US Patents, China's latest patents, Technical Efficacy Thesaurus, Application Domain, Technology Topic, Popular Technical Reports.
© 2025 PatSnap. All rights reserved.Legal|Privacy policy|Modern Slavery Act Transparency Statement|Sitemap|About US| Contact US: help@patsnap.com