Magnesium oxide-metal sulfide-biomass charcoal composite material as well as preparation method and application thereof
A technology of metal sulfide and biochar, applied in chemical instruments and methods, chemical/physical processes, water treatment of special compounds, etc., to achieve low thermal expansion coefficient, rich pore structure, and excellent adsorption effect
- Summary
- Abstract
- Description
- Claims
- Application Information
AI Technical Summary
Problems solved by technology
Method used
Image
Examples
preparation example Construction
[0039] The embodiment of the present invention also provides a preparation method of magnesium oxide-metal sulfide-biomass charcoal composite material as described above, refer to figure 1 , the preparation method comprises:
[0040] Step S10, dissolving the biomass waste, bischofolite, monovalent metal salt and nitrogen source organic matter in a solvent, stirring and mixing, heating to evaporate the solvent, and obtaining a mixed material.
[0041] Preferably, the biomass waste is crop straw, the main component of the crop straw is biomass carbon, which needs to be pulverized first; the bischofolite is a by-product of the potassium extraction process, and the main component is magnesium chloride hexahydrate ; The monovalent metal salt is silver nitrate, silver chloride, silver sulfate, cuprous chloride or cuprous sulfate; the nitrogen source organic matter is melamine, urea or polyvinylpyrrolidone.
[0042] Further preferably, in terms of parts by mass, the mass fraction of...
Embodiment 1
[0065] Step 1, take by weighing 75g of pulverized rice straw, 15g of potassium extract by-product bischolite, 2g of silver nitrate and 8g of melamine are placed in a batching tank filled with 600mL of deionized water, and at room temperature with a rotating speed of 300 r / Min was stirred for 0.5h. The temperature of the mixed suspension in the batching tank was raised to 60° C. and stirred at a constant temperature until the deionized water was completely evaporated to obtain a mixed material.
[0066] Step 2: Add 20g of potassium hydroxide to the mixed material, stir evenly and put it into a high-temperature converter with a rotation speed of 10 r / min, and feed H 2 H with a volume fraction of S of 25% and a gas flow rate of 80 mL / min 2 S / N 2 The air in the furnace was exhausted with the mixed gas, and the temperature was raised to 600°C at a rate of 10°C / min under the atmosphere and roasted at a constant temperature for 3 hours to obtain a roasted product.
[0067] The wa...
Embodiment 2
[0072] Step 1. Weigh 70g of pulverized wheat straw, 13g of potassium-extracting by-product bischolite, 2g of cuprous chloride and 15g of urea into a batching tank filled with 550mL of deionized water, and at room temperature at a speed of Stir at 250 r / min for 0.5h. The temperature of the mixed suspension in the batching tank was raised to 65° C. and stirred at a constant temperature until the deionized water was completely evaporated to obtain a mixed material.
[0073] Step 2: Add 15g of potassium hydroxide to the mixed material, stir evenly and put it into a high-temperature converter with a rotation speed of 10 r / min, and feed H 2 H with a volume fraction of S of 30% and a gas flow rate of 70 mL / min 2 S / N 2 The mixed gas exhausted the air in the furnace, and in this atmosphere, the temperature was raised to 650°C at 15°C / min and roasted at a constant temperature for 2.5h to obtain a roasted product.
[0074] The waste gas generated during the reaction process is absorbe...
PUM
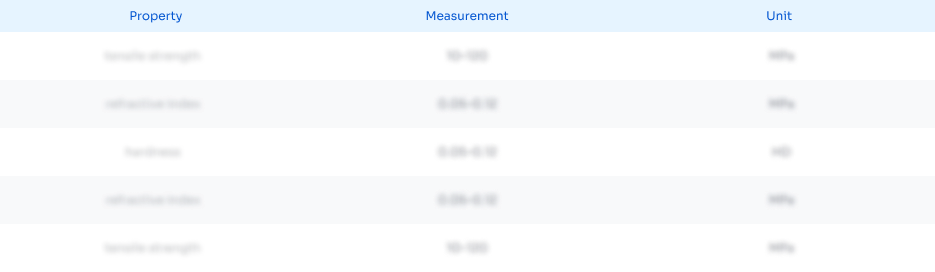
Abstract
Description
Claims
Application Information

- R&D Engineer
- R&D Manager
- IP Professional
- Industry Leading Data Capabilities
- Powerful AI technology
- Patent DNA Extraction
Browse by: Latest US Patents, China's latest patents, Technical Efficacy Thesaurus, Application Domain, Technology Topic, Popular Technical Reports.
© 2024 PatSnap. All rights reserved.Legal|Privacy policy|Modern Slavery Act Transparency Statement|Sitemap|About US| Contact US: help@patsnap.com